[Precision Tube making equipment]Exploring Precision Tube Making Equipment: Advancements, Applications, and Industry Trends Driving Efficiency in Manufacturing Processes
News 2025-1-13
Precision tube making equipment has become a cornerstone of modern manufacturing technologies, revolutionizing how industries produce various types of tubes and pipes for different applications. With the rapid growth of sectors like automotive, aerospace, medical devices, and energy, the demand for high-quality, precise, and durable tubes has surged. This article delves into the advancements in precision tube making equipment, its wide-ranging applications, and the current trends driving the industry forward.
Understanding Precision Tube Making Equipment
Precision tube making equipment encompasses a variety of machines and processes designed to manufacture tubes with exact dimensions and tolerances. This equipment includes tube rolling machines, cutting machines, bending machines, welding systems, and even testing apparatuses to ensure the final product meets stringent industry standards.
The primary aim of these machines is to control the diameter, wall thickness, length, and overall geometry of the tubes produced. Achieving such precision is crucial, particularly in industries where the slightest deviation can lead to significant performance issues or safety hazards.
Recent Advancements in Technology
Over the past few years, precision tube making equipment has seen considerable technological advancements. One of the most significant developments is the integration of automation and robotics into the manufacturing process. Automated systems can operate high-speed tube machinery with minimal human intervention, enhancing productivity and reducing labor costs. Moreover, these advancements have increased flexibility, enabling manufacturers to produce small batches or customize orders without the need for extensive retooling.
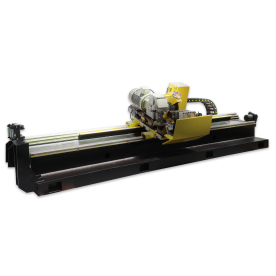
Exploring Precision Tube Making Equipment: Advancements, Applications, and Industry Trends Driving Efficiency in Manufacturing Processes

Exploring Precision Tube Making Equipment: Advancements, Applications, and Industry Trends Driving Efficiency in Manufacturing Processes

Exploring Precision Tube Making Equipment: Advancements, Applications, and Industry Trends Driving Efficiency in Manufacturing Processes
The applications of precision tubes are vast and varied. In the **automotive industry**, precision tubes are crucial for components like fuel lines, exhaust systems, and chassis. The growing trend towards lightweight vehicles has increased the demand for high-strength, lightweight tubes, often made from materials like aluminum and specialized alloys.
In the **aerospace sector**, precision tubes are used in hydraulic systems, fuel lines, and structural components. The stringent safety regulations and performance requirements make precision manufacturing paramount in this field. Advanced engineering techniques and materials are essential for meeting the demands of flight safety and fuel efficiency.
The **medical device sector** heavily relies on precision tube making equipment to manufacture products like catheters, stents, and surgical instruments. These applications necessitate strict adherence to hygiene and quality standards, making the precision of manufacturing processes critical.
Furthermore, in the **energy sector**, precision tubes are utilized for transporting fluids in oil and gas operations and for structural applications like pipelines and offshore platforms. The extreme conditions under which these tubes operate necessitate robust construction, often requiring specialized manufacturing techniques.
Industry Trends Driving Innovation
Several trends are shaping the future of precision tube making equipment. Firstly, the push for sustainability is leading manufacturers to seek eco-friendly materials and processes. This involves minimizing waste, recycling materials, and implementing energy-efficient manufacturing practices.
Secondly, the demand for customization and rapid prototyping is on the rise. Today’s consumers expect tailored solutions, prompting manufacturers to adopt flexible production methods, often enabled by digital technologies and advanced software.
Lastly, the drive towards Industry 4.0—a trend characterized by the Internet of Things (IoT) and smart manufacturing—means that precision tube making equipment is becoming increasingly interconnected. This connectivity allows for real-time data analytics and machine learning, optimizing performance and predictive maintenance.
Conclusion
In conclusion, precision tube making equipment is integral to various industries, supporting the production of components that demand unparalleled accuracy and reliability. With continuous advancements in technology and shifting industry trends towards automation, sustainability, and customization, the future of precision tube manufacturing looks promising. As companies adapt and evolve in response to these changes, the importance of precision manufacturing will only grow, solidifying its position as a vital component within modern manufacturing ecosystems.