[Precision Solid state HF welder]Exploring the Advantages and Applications of Precision Solid State HF Welders in Modern Manufacturing Processes
News 2025-1-13
In the realm of modern manufacturing, the quest for efficiency, accuracy, and versatility has led to the development of various welding technologies. Among these, the Precision Solid State HF Welder has emerged as a game-changer, offering numerous benefits that cater to the diverse needs of the industry. This article delves into the workings, advantages, and applications of Precision Solid State HF Welders, highlighting why they are increasingly becoming the go-to option for manufacturers worldwide.
What is a Precision Solid State HF Welder?
A Precision Solid State HF Welder is a welding device that employs high-frequency electrical currents to join materials, typically metals and plastics, with exceptional precision and minimal thermal distortion. Unlike other welding methods that rely on traditional transformer technology, solid-state HF welders utilize solid-state components, which offer several exponential advantages. The high-frequency electromagnetic waves penetrate the materials being joined, creating localized heating, which results in a strong and durable bond.
Key Advantages of Precision Solid State HF Welders
1. **High Efficiency**: One of the defining characteristics of solid-state HF welders is their energy efficiency. These machines require less power compared to traditional welding technologies, as they convert electrical energy to thermal energy with minimal losses. This not only reduces operational costs but also lessens the environmental impact.
2. **Precision and Control**: Precision is paramount in welding, and solid-state HF welding technology excels in this regard. With advanced control systems, operators can finely tune parameters such as frequency, power output, and welding duration. This makes it possible to achieve consistent results across multiple applications, even when joining diverse materials.
3. **Reduced Thermal Impact**: Traditional welding processes often generate excessive heat, which can lead to distortion, structural integrity issues, and increased post-weld treatment requirements. In contrast, the localized heating mechanism of Precision Solid State HF Welders minimizes the heat-affected zone (HAZ), ensuring that surrounding materials remain intact and undamaged.
4. **Compact Design**: Solid-state HF welders have a compact and modular design, which is advantageous for manufacturers with limited floor space. Their smaller footprint and ease of integration into existing production lines make them an appealing option for numerous industries.
5. **Adaptability**: The versatility of Precision Solid State HF Welders allows them to be used for various welding processes, including seam welding, spot welding, and even plastic welding. This adaptability makes them suitable for a wide range of industries, from automotive to textiles and electronics.
6. **Low Maintenance Needs**: With fewer moving parts and the use of durable solid-state components, these welders require less maintenance and have a longer operational lifespan. This translates into lower downtime and higher productivity for manufacturers.
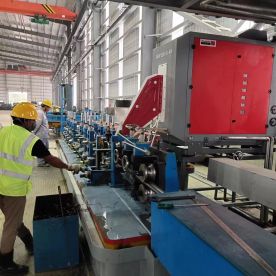
Exploring the Advantages and Applications of Precision Solid State HF Welders in Modern Manufacturing Processes
The applications of Precision Solid State HF Welders are vast and varied, demonstrating their crucial role in contemporary manufacturing:
1. **Automotive Industry**: In automotive manufacturing, these welders are increasingly used for joining various components, including harnesses, body panels, and other lightweight materials that are essential for fuel efficiency.
2. **Electronics**: The electronics sector benefits from the precise and gentle nature of solid-state HF welding. It is employed in assembling circuit boards, connectors, and other sensitive components where temperature control is critical.
3. **Textiles and Packaging**: Precision Solid State HF Welders are revolutionizing the textile industry through welded seams in technical textiles and non-woven materials. Additionally, they play a role in producing heat-sealed packaging that extends product shelf life.
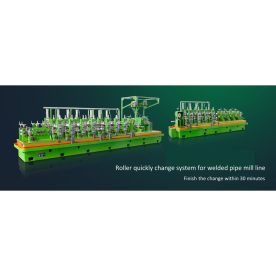
Exploring the Advantages and Applications of Precision Solid State HF Welders in Modern Manufacturing Processes
5. **Medical Device Manufacturing**: The medical field mandates stringent quality controls, and solid-state HF welders help ensure that delicate medical devices are produced with maximum accuracy and clean welds, ensuring no contamination.
Conclusion
