[Solid state HF welder with temperature control]Exploring the Benefits and Applications of Solid State HF Welder with Temperature Control in Modern Manufacturing Techniques
News 2025-1-12
****In the ever-evolving landscape of manufacturing, the need for precise and efficient welding techniques has never been more critical. Among the various technologies available, the solid state high-frequency (HF) welder with temperature control stands out as a revolutionary development. This advanced welding system not only enhances the quality of welds but also improves the overall productivity of the manufacturing process. In this article, we will delve into the features, benefits, and applications of solid state HF welders equipped with temperature control, highlighting their significance in contemporary production environments.
Understanding Solid State HF Welding
Solid state HF welding is a sophisticated process that uses high-frequency electromagnetic energy to generate heat, which is critical for fusing materials together. Unlike traditional welding techniques that rely on external heating sources, such as gas flames or arc welders, solid state welding utilizes the properties of electromagnetism to heat the metal at the molecular level. This method is not only faster but also provides higher precision and control over the welding process.
The Role of Temperature Control
One of the key advancements in solid state HF welding is the integration of temperature control systems. These systems monitor the temperature of the welded material in real-time, allowing for precise adjustments during the welding process. The importance of temperature control cannot be overstated; it ensures that the materials reach the optimal temperature for welding without overheating, which can cause deformities, weaken the integrity of the weld, or even damage the materials themselves.
By maintaining the ideal welding temperature, manufacturers can achieve uniform welds with consistent quality across multiple products. This level of control not only enhances the structural integrity of the final product but also reduces the likelihood of defects and rework, ultimately leading to cost savings and improved efficiency.
Benefits of Solid State HF Welders with Temperature Control
1. **Increased Precision**: The combination of solid state technology and temperature control allows for greater precision in welding operations. Manufacturers can create intricate assemblies with tight tolerances, essential for industries where even the smallest imperfections can lead to failure.
2. **Energy Efficiency**: Solid state HF welders consume significantly less power compared to traditional welding methods. The rapid heating and cooling cycles mean that energy is used more efficiently, reducing the overall carbon footprint of the production process.
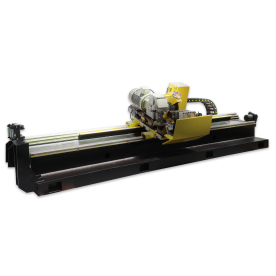
Exploring the Benefits and Applications of Solid State HF Welder with Temperature Control in Modern Manufacturing Techniques
4. **Reduction in Heat Affected Zones (HAZ)**: Traditional welding methods often create extensive heat-affected zones, which can compromise the strength and properties of the surrounding material. Solid state HF welding minimizes HAZ due to its efficient heating process, preserving the integrity of the base materials.
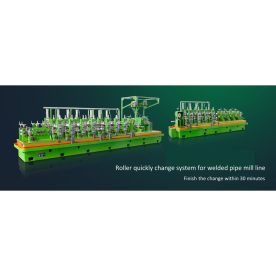
Exploring the Benefits and Applications of Solid State HF Welder with Temperature Control in Modern Manufacturing Techniques
Applications in Industry
Solid state HF welders with temperature control find applications across various industries, including:

Exploring the Benefits and Applications of Solid State HF Welder with Temperature Control in Modern Manufacturing Techniques
Conclusion
The advent of solid state HF welders with temperature control represents a significant leap forward in manufacturing technology. By offering precision, energy efficiency, and enhanced material compatibility, this innovative welding solution meets the diverse needs of modern industries. As manufacturers continue to embrace advanced technologies to improve efficiency and product quality, solid state HF welding with temperature control is poised to play a crucial role in shaping the future of production processes. Embracing this technology not only enhances operational efficiency but also paves the way for innovation and competitiveness in an increasingly demanding marketplace.