[Stainless steel pipe mill production line]Exploring the Innovations and Efficiency of the Stainless Steel Pipe Mill Production Line for Modern Manufacturing Industries
News 2025-1-12
Stainless steel pipes have become a critical component in various industries, including construction, automotive, oil and gas, and pharmaceuticals. The stainless steel pipe mill production line represents an advanced technology that plays a significant role in meeting the growing demand for these durable and versatile pipes. This article delves into the innovations, processes, benefits, and challenges associated with the stainless steel pipe mill production line, highlighting its importance in modern manufacturing.
Understanding the Stainless Steel Pipe Mill Production Line
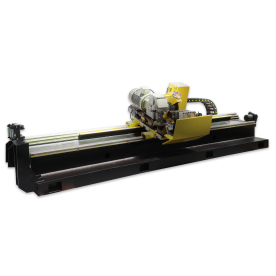
Exploring the Innovations and Efficiency of the Stainless Steel Pipe Mill Production Line for Modern Manufacturing Industries
Key Stages of Production
1. **Raw Material Preparation**: The process begins with the selection of stainless steel slabs or billets, which are carefully inspected for quality. These materials are often chosen based on the desired properties of the final product, such as corrosion resistance, strength, and weldability.
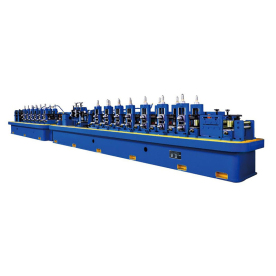
Exploring the Innovations and Efficiency of the Stainless Steel Pipe Mill Production Line for Modern Manufacturing Industries
3. **Welding**: For certain types of pipes, particularly those with larger diameters, welding becomes necessary. Techniques like TIG (Tungsten Inert Gas) and MIG (Metal Inert Gas) welding are commonly employed. The welding process ensures that the pipes are structurally sound and meet the required specifications.
4. **Cooling**: After welding, the pipes must be cooled back down to room temperature to stabilize their structure. This is typically done using water sprays or air cooling, depending on the specific requirements of the product.
5. **Finishing**: This stage involves processes such as straightening, cutting the pipes to specific lengths, and applying surface finishes. Polishing and coating may also be performed to enhance the aesthetic appeal and corrosion resistance of the pipes.
6. **Quality Control**: The final step in the production line is rigorous quality control, which involves testing the pipes for strength, dimensions, and tolerances. Non-destructive testing methods, such as ultrasonic testing or eddy current testing, are often employed to ensure the integrity of the products.
Benefits of the Stainless Steel Pipe Mill Production Line
The stainless steel pipe mill production line offers several advantages that are crucial for modern manufacturing.
- **High Efficiency**: The automation and advanced machinery used in the production line significantly increase output rates, allowing companies to meet high demand without compromising quality. - **Versatility**: This production line can be adapted to produce a variety of pipe sizes, shapes, and grades, making it suitable for diverse applications. - **Cost-effectiveness**: Despite the high initial investment, the streamlined processes and reduced waste lead to lower operating costs in the long run. - **Environmentally Friendly**: The production techniques often emphasize recycling and the use of eco-friendly practices, contributing to sustainability goals.
Challenges Faced by the Industry
Despite its benefits, the stainless steel pipe mill production line faces several challenges.
- **Equipment Investment**: The setup of a state-of-the-art production line requires substantial capital investment, which may be a barrier for small manufacturers. - **Skilled Labor**: Operating and maintaining the advanced machinery requires skilled labor, which may not always be readily available. - **Market Fluctuations**: The stainless steel market is subject to fluctuations in prices and demand, which can impact production costs and profit margins.
Conclusion
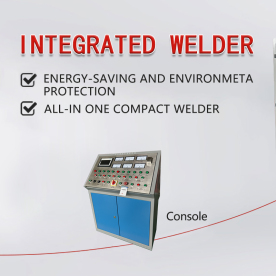