[IF pipe seam annealing machine ]Revolutionizing Metal Processing: A Comprehensive Overview of the IF Pipe Seam Annealing Machine and Its Impact on Manufacturing Efficiency
News 2025-1-11
In the ever-evolving landscape of manufacturing and metal processing, the need for enhanced efficiency and quality in production methods is paramount. One of the innovations that has emerged to meet these demands is the IF pipe seam annealing machine. This sophisticated piece of equipment is designed specifically to improve the integrity and performance of welded pipes, making it indispensable in various industries, including oil and gas, construction, and automotive manufacturing.
Understanding Pipe Seam Annealing
Before delving into the specifics of the IF pipe seam annealing machine, it's essential to understand what pipe seam annealing entails. Annealing is a heat treatment process designed to alter the physical and sometimes chemical properties of a material. The primary purpose of this procedure is to reduce hardness, increase ductility, and help eliminate internal stresses, thereby improving the material's workability and structural integrity.
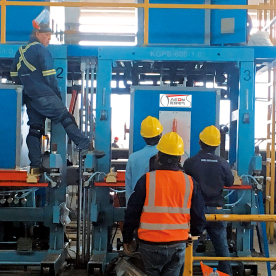
Revolutionizing Metal Processing: A Comprehensive Overview of the IF Pipe Seam Annealing Machine and Its Impact on Manufacturing Efficiency
Features and Specifications of the IF Pipe Seam Annealing Machine
The IF pipe seam annealing machine is equipped with several advanced features that set it apart from traditional annealing methods.
1. **Induction Heating Technology**: The machine employs induction heating, a method that uses electromagnetic fields to generate heat within the material itself. This technique is highly efficient, as it significantly reduces energy consumption and minimizes heat loss compared to conventional heating methods.
2. **Automation and Control Systems**: Modern IF pipe seam annealing machines come equipped with sophisticated control systems that allow for precise monitoring and adjustment of heating parameters. These features enable operators to achieve consistent and repeatable results, which is crucial in maintaining product quality.
3. **Versatility**: The IF pipe seam annealing machine is versatile and can handle pipes of various sizes and materials, including carbon steel, stainless steel, and even exotic alloys. This adaptability makes it a valuable addition to any manufacturing facility.
4. **Safety Features**: Safety is always a concern when dealing with high-temperature processes. The design of the IF pipe seam annealing machine incorporates several safety features, including emergency shut-off mechanisms and robust shielding to protect operators from heat and electromagnetic fields.
Benefits of Using the IF Pipe Seam Annealing Machine
The introduction of the IF pipe seam annealing machine into a manufacturing process brings numerous advantages:
1. **Enhanced Material Properties**: With precise control over the annealing process, the machine provides improved material properties, including greater tensile strength and ductility. This results in pipes that can withstand higher pressures and harsher environments.
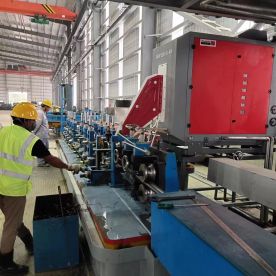
Revolutionizing Metal Processing: A Comprehensive Overview of the IF Pipe Seam Annealing Machine and Its Impact on Manufacturing Efficiency
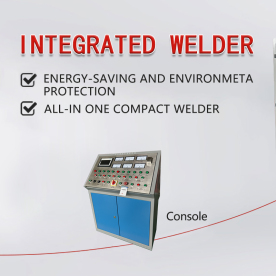
Revolutionizing Metal Processing: A Comprehensive Overview of the IF Pipe Seam Annealing Machine and Its Impact on Manufacturing Efficiency
3. **Decreased Defect Rates**: By treating welded seams properly, the IF pipe seam annealing machine helps minimize the occurrence of defects such as cracks and weak points, thereby reducing the risk of failures in the field.
4. **Better Customer Satisfaction**: The high-quality output produced by annealed pipes can lead to increased customer satisfaction and trust in products, which is critical for businesses aiming to maintain a competitive edge in the market.
Conclusion
In conclusion, the IF pipe seam annealing machine represents a significant advancement in the field of metallurgy and manufacturing. By employing state-of-the-art induction heating technology and an array of automated features, this machine not only enhances the quality of welded pipes but also contributes to greater efficiencies and cost savings for manufacturers. For industries that rely heavily on the performance of welded pipes, the adoption of the IF pipe seam annealing machine is a step towards achieving higher standards and longevity in their products. As the industry continues to evolve, embracing such innovative technologies will be key to remaining competitive in a global market.