[Solid state high frequency welder]Revolutionizing Metal Fabrication: The Advantages and Applications of Solid State High Frequency Welders in Modern Manufacturing
News 2025-1-11
In the world of manufacturing, the need for efficient, high-quality metal fabrication techniques has never been more essential. Amidst an array of welding technologies, the solid state high frequency welder has emerged as a transformative solution for various industries. This innovative technology combines the principles of solid-state electronics with high-frequency welding processes to deliver unparalleled results in terms of precision, speed, and energy efficiency. In this article, we will explore the workings of solid state high frequency welders, their benefits, and the myriad applications that make them an invaluable asset in modern manufacturing.
Understanding Solid State High Frequency Welders
Solid state high frequency welding is a process that utilizes high-frequency electrical currents to generate heat through the resistance of metal parts that are to be joined together. Unlike traditional welding methods that rely on arc welding or gas to produce heat, solid state high frequency welders employ solid-state electronics to create an electromagnetic field. This electromagnetic field induces currents within the metal, causing it to heat up rapidly and allowing for efficient bonding between materials.
These welders are equipped with semiconductor devices that are capable of controlling and modulating the flow of electricity. This technology allows for greater precision in managing the welding process, enabling manufacturers to fine-tune parameters such as temperature, pressure, and welding time. As a result, users can achieve consistent and high-quality welds, minimizing the likelihood of defects and enhancing overall product durability.
Benefits of Solid State High Frequency Welders
The advantages of solid state high frequency welders are numerous and contribute significantly to their growing popularity in various industrial applications. Here are some key benefits:
1. **Energy Efficiency:** Solid state high frequency welders are designed to consume less energy compared to traditional welding machines. The ability to harness high-frequency currents means that a lower amount of power is needed to achieve the desired welding results. This not only reduces operational costs but also minimizes the environmental impact of metal fabrication processes.
2. **Precision and Control:** The advanced technology of solid state welders grants operators exceptional control over the welding parameters. This precision is particularly beneficial when working with thin materials that require accurate heat application to avoid warping or damage. The ability to customize settings also allows manufacturers to adapt their welding processes for various types of metals and thicknesses.
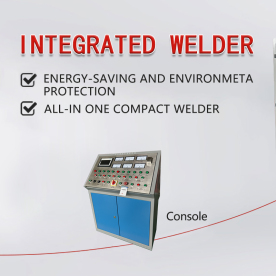
Revolutionizing Metal Fabrication: The Advantages and Applications of Solid State High Frequency Welders in Modern Manufacturing
4. **Improved Weld Quality:** With a more controlled and efficient heating process, solid state high frequency welders produce welds that are stronger and more reliable. The minimized risk of oxidation and contamination during the welding process contributes to the superior structural integrity of the welded joints.
5. **Versatility:** Solid state welders can be used with a variety of materials, including metals such as copper, aluminum, and stainless steel. This versatility makes them suitable for numerous applications, ranging from automotive and aerospace manufacturing to the production of electronic components.
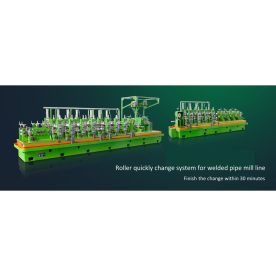
Revolutionizing Metal Fabrication: The Advantages and Applications of Solid State High Frequency Welders in Modern Manufacturing
Solid state high frequency welders have found a diverse range of applications across various industries, highlighting their versatility and effectiveness.
- **Automotive Industry:** In automotive manufacturing, solid state welding is utilized for joining components such as exhaust systems, fuel lines, and structural parts, where high integrity and performance are essential.
- **Aerospace Sector:** The aerospace industry leverages solid state welding for applications requiring lightweight and robust materials. High-frequency welding is ideal for creating intricate components while maintaining stringent safety standards.

Revolutionizing Metal Fabrication: The Advantages and Applications of Solid State High Frequency Welders in Modern Manufacturing
- **Tube and Pipe Fabrication:** Industries engaged in tube and pipe fabrication frequently utilize solid state welding for producing high-strength joints essential for transporting fluids and gases.
Conclusion
As the manufacturing landscape continues to evolve, the solid state high frequency welder stands out as a pivotal technology driving innovation in metal fabrication. Its energy efficiency, precision, and versatility make it a formidable choice for a wide range of industries, allowing manufacturers to enhance productivity while minimizing costs and environmental impact. With the ongoing advancements in solid-state electronics, the future of welding appears brighter than ever, promising even more remarkable developments in the realm of high-frequency welding technology.