[Industrial All-in-one High Frequency Welder]Unlocking Efficiency and Precision in Manufacturing with the Industrial All-in-one High Frequency Welder: A Comprehensive Guide
News 2025-1-10
In the ever-evolving landscape of manufacturing, the demand for efficient and precise production methods has never been greater. Industries are continuously seeking ways to enhance their processes while minimizing costs and maximizing output. One such technological innovation that has gained immense popularity is the Industrial All-in-one High Frequency Welder. This specialized equipment is designed to streamline operations, ensuring high-quality results in various applications, from fabricating textiles to assembling electronic components. In this article, we delve into the key features, benefits, and various applications of the Industrial All-in-one High Frequency Welder, highlighting its importance in modern manufacturing.
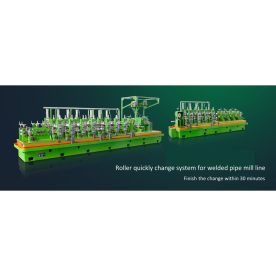
Unlocking Efficiency and Precision in Manufacturing with the Industrial All-in-one High Frequency Welder: A Comprehensive Guide
High frequency welding, also known as RF welding or dielectric welding, is a process that uses high-frequency electromagnetic waves to heat up and bond materials together. This technique is widely utilized for thermoplastic materials, which soften upon heating, allowing for exceptional adhesion without the need for additional adhesives. The Industrial All-in-one High Frequency Welder is engineered to handle diverse welding requirements, making it a versatile asset for manufacturers.
Key Features of the Industrial All-in-one High Frequency Welder
1. **Versatility**: One of the standout features of this welder is its ability to work with a variety of materials, including PVC, polyurethane, polyethylene, and many other thermoplastics. This versatility allows manufacturers to use a single machine for multiple applications, reducing the need for various specialty welders.
2. **Precision**: The advanced controls and monitoring systems integrated into the Industrial All-in-one High Frequency Welder ensure precision in temperature and pressure. This precision is crucial for achieving strong, durable welds while minimizing the risk of overheating or damaging materials.
3. **Efficiency**: The high welding speed associated with this equipment significantly boosts production efficiency. Faster welding times mean shorter cycles and increased output, which can lead to substantial cost savings for manufacturers.
4. **User-friendly Interface**: Most modern Industrial All-in-one High Frequency Welders come equipped with intuitive control panels that enable operators to easily set and adjust welding parameters. This user-friendly design minimizes the learning curve and enhances operational efficiency.

Unlocking Efficiency and Precision in Manufacturing with the Industrial All-in-one High Frequency Welder: A Comprehensive Guide
Applications in Various Industries
The Industrial All-in-one High Frequency Welder is employed across a multitude of industries, showcasing its adaptability and functionality. Here are some notable applications:
1. **Textile Industry**: In the textile sector, this welder is commonly used to create seams and joints in synthetic materials. It is particularly effective in manufacturing items such as inflatable structures, automotive interiors, and medical textiles, where strong and durable seams are essential.
2. **Electronics Manufacturing**: The high-frequency welding process is utilized in assembling electronic products, such as casings and covers, ensuring that the components are securely bonded without introducing contaminants that could affect performance.
3. **Packaging Industry**: This technology is instrumental in the production of heat-sealed packaging, which is crucial for preserving the freshness of food products. The high-frequency welder enables manufacturers to create reliable seals that extend shelf life.
4. **Automotive and Aerospace**: In these sectors, the Industrial All-in-one High Frequency Welder is used for welding various components, including trim and insulation materials. The ability to create strong, lightweight bonds is vital for vehicle performance and safety.
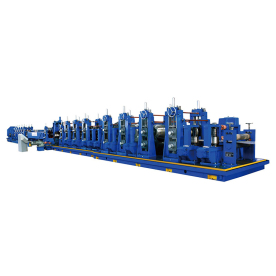
Unlocking Efficiency and Precision in Manufacturing with the Industrial All-in-one High Frequency Welder: A Comprehensive Guide
- **Cost Savings**: By reducing the material waste typically associated with traditional welding methods and speeding up production times, manufacturers can experience significant cost savings.
- **Enhanced Quality**: The precise control afforded by the high-frequency welding process results in high-quality welds that are often superior to those achieved with conventional welding methods.
- **Environmentally Friendly**: The absence of adhesives in the welding process makes it a more environmentally friendly option compared to other methods that require chemical bonding materials.
Conclusion
The Industrial All-in-one High Frequency Welder stands out as a transformative piece of equipment in the manufacturing realm. Its versatility, efficiency, and precision make it an invaluable asset for various industries seeking to improve their production processes. As manufacturers continue to adapt to technological advancements, embracing devices like the Industrial All-in-one High Frequency Welder will undoubtedly pave the way for greater efficiency and enhanced product quality in the future. Investing in this technology not only streamlines operations but also positions businesses for success in a competitive market.