[Roller for tube mill]Understanding the Role of Roller in Tube Mill Operations: Enhancing Efficiency and Quality in Metal Fabrication Processes
News 2025-1-10
In the realm of metal fabrication, tube mills play a critical role in producing various types of tubes and pipes utilized across diverse industries. A vital component of tube mills is the roller, which serves multiple functions within the manufacturing process. Understanding the role of rollers in tube mills is essential for optimizing production efficiency, ensuring consistent quality, and prolonging equipment lifespan. This article delves into the importance of rollers in tube mill operations, their types, operational considerations, and best practices for maintenance.
The Function of Rollers in Tube Mills
At its core, the tube mill is designed to convert flat metal strips into round tubes, and the rollers are the key elements facilitating this transformation. They carry out several functions, including shaping, welding, sizing, and finishing the tubes. The primary role of rollers in tube mills can be summarized as follows:
1. **Forming**: Rollers shape the flat metal strips into tubular forms through a series of calibrated passes. Each set of rollers is carefully designed to perform specific tasks, ensuring that the strip is gradually bent into the desired shape without compromising its integrity.
2. **Welding**: In many tube mills, rollers are also equipped with welding capabilities. As the strip reaches the final stage of forming, it is often welded along the edges to create a closed seam. The rollers apply heat and pressure necessary for effective welding, ensuring a strong bond.
3. **Sizing**: After the welding process, tubes must be sized to meet specific standards. Rollers are integral to sizing mills that enable accurate diameter and wall thickness measurements, which are crucial for ensuring that the final product meets market specifications.
4. **Finishing**: Once the tubes have been formed and sized, they often go through a finishing process. Rollers assist in smoothing and polishing the surface of the tubes, eliminating rough edges, and preparing them for packaging.
Types of Rollers Used in Tube Mills
Rollers in tube mills come in various designs and materials, tailored to the specific requirements of the manufacturing process. Some common types include:
- **Entry Rollers**: These initial rollers guide the metal strip into the tube mill and initiate the shaping process. They need to be highly durable to withstand the stress of incoming materials.
- **Forming Rollers**: These are typically arranged in sets and are designed to progressively bend the strip into a tubular shape. The configuration of forming rollers varies based on the diameter and thickness of the final tube.
- **Welding Rollers**: Often integrated with welding stations, these rollers create pressure and heat during the welding process, facilitating the fusion of the tube edges.
- **Sizing Rollers**: Once the tubes are welded, sizing rollers ensure they adhere to precise measurements, playing a vital role in maintaining product quality.
- **Finishing Rollers**: These rollers are used toward the end of the production line to enhance the surface quality of the tubes, removing any imperfections that may have arisen during earlier processes.
Operational Considerations
Roller efficiency is paramount in tube mills, and several operational factors impact their performance:
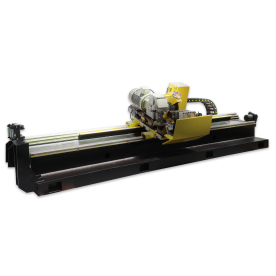
Understanding the Role of Roller in Tube Mill Operations: Enhancing Efficiency and Quality in Metal Fabrication Processes
- **Roller Alignment**: Proper alignment of rollers is essential to achieve uniform pressure and avoid excessive wear. Misalignments can lead to defects in the tube, such as inconsistent wall thickness or shape.
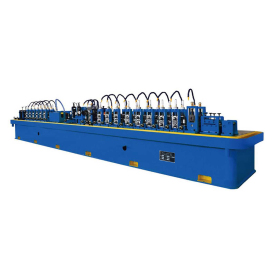
Understanding the Role of Roller in Tube Mill Operations: Enhancing Efficiency and Quality in Metal Fabrication Processes
Best Practices for Roller Maintenance
Maintaining the rollers in tube mills is crucial for continued operational efficiency and product quality. Here are some best practices:
1. **Regular Inspection**: Conduct periodic inspections of rollers to check for signs of wear, misalignment, or damage. Early detection can prevent costly downtimes.
2. **Proper Lubrication**: Adequate lubrication reduces friction between rollers, minimizing wear and tear while enhancing performance.

Understanding the Role of Roller in Tube Mill Operations: Enhancing Efficiency and Quality in Metal Fabrication Processes
4. **Training Staff**: Operators should receive training on the operational and maintenance practices specific to rollers to ensure effective handling and usage.
In conclusion, the roller plays a pivotal role in tube mill operations, significantly influencing product quality and production efficiency. By understanding their functions, types, operational considerations, and maintenance practices, manufacturers can optimize their tube mill operations and achieve better outcomes in their metal fabrication processes. As industries continue to evolve, the need for high-quality tubing will grow, making it essential to invest in reliable roller technology and practices.