[Precision Mould for Tube Mills]Enhancing the Efficiency of Tube Mills with Precision Mould Innovations for Superior Manufacturing Quality
News 2025-1-8
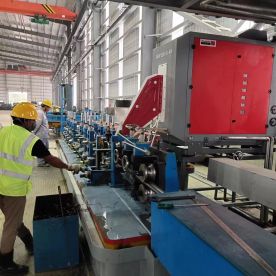
Enhancing the Efficiency of Tube Mills with Precision Mould Innovations for Superior Manufacturing Quality
Understanding Tube Mills
Tube mills are specialized machinery that manufacture tubes from steel or other materials. They bend the material into a cylindrical shape, followed by the welding of the edges to create a seamless tube. These mills are widely used in various industries, including construction, automotive, and energy, and are integral to producing structural components, fluid pipes, and more.
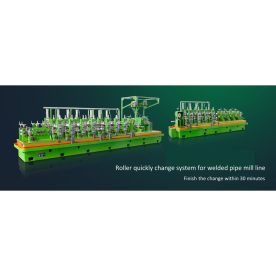
Enhancing the Efficiency of Tube Mills with Precision Mould Innovations for Superior Manufacturing Quality
The Importance of Precision Moulds
Precision moulds are engineered to provide exact specifications, ensuring that tubes maintain consistent dimensions and high structural integrity during manufacture. A well-designed mould minimizes deviations in shape and size, which can lead to defects such as irregularities, weak spots, or even catastrophic failures in practical application.
For tube mills, precision moulds not only enhance the aesthetic qualities of the finished product but also optimize performance under different conditions. For instance, tubes used in high-pressure applications, such as gas pipelines, require a higher degree of precision to withstand external and internal stresses without compromising safety.
Innovations in Precision Mould Technology
Recent advancements in technology have led to significant improvements in the design and manufacturing of precision moulds for tube mills. These innovations include 3D printing and CNC machining, which allow for highly detailed designs that were previously unattainable using traditional methods.
1. 3D Printing for Prototyping and Production
3D printing has revolutionized the prototyping phase of mould design. Manufacturers can now produce high-definition models of moulds quickly and cost-effectively. This process saves time and reduces material waste, allowing for frequent modifications and enhanced feedback integration. Consequently, the final product is optimized for performance before it even enters the production phase.
2. CNC Machining for Unparalleled Precision
CNC (Computer Numerical Control) machining has also transformed the manufacturing of precision moulds. This technology ensures high accuracy in the creation of moulds, providing a level of detail that is difficult to achieve manually. CNC machines can produce intricate designs that meet the demanding specifications of tube mills, ensuring each component fits perfectly and functions as intended.
Enhancing Efficiency in Tube Mills

Enhancing the Efficiency of Tube Mills with Precision Mould Innovations for Superior Manufacturing Quality
By focusing on precision during the mould design and manufacturing process, companies can also contribute to sustainability efforts. Efficient production means lower energy consumption and reduced waste, aligning with global targets for environmentally responsible manufacturing practices.
Conclusion
In conclusion, the role of precision moulds in tube mills cannot be overstated. They are an integral component that directly influences both the quality of the final product and the overall efficiency of the manufacturing process. As technology continues to evolve, innovations in mould design and manufacturing are set to enhance the capabilities of tube mills even further. Embracing these advancements will not only yield superior products but also drive the industry towards a more sustainable and efficient future. With precision moulds paving the way, the future of tube manufacturing looks bright and promising.