[Customized ERW tube mill solutions]Exploring the Advantages of Customized ERW Tube Mill Solutions for Enhanced Manufacturing Efficiency and Product Quality
News 2025-1-8
In the world of manufacturing, the demand for high-quality, precision-engineered steel tubes has never been higher. As industries evolve and adapt to newer technologies, the need for Customized Electric Resistance Welded (ERW) tube mill solutions has become paramount. Customized ERW tube mills are designed to meet specific production requirements and increase overall operational efficiency. This article dives into the advantages of adopting customized ERW tube mill solutions, exploring their role in enhancing manufacturing capabilities and product quality while also showcasing the importance of tailor-made machinery in today’s competitive landscape.
Electric Resistance Welding (ERW) has gained substantial traction due to its cost-effectiveness and ability to produce high-strength steel tubes for various applications. However, standard ERW tube mill configurations may not be suitable for all manufacturers, given the diverse needs across different sectors. Customized ERW tube mills enable companies to optimize their production processes, streamline operations, and reduce waste, making them a viable choice for industries such as automotive, construction, oil and gas, and aerospace.
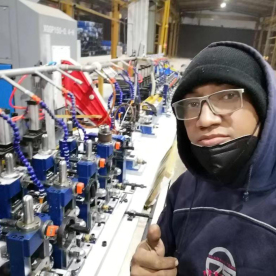
Exploring the Advantages of Customized ERW Tube Mill Solutions for Enhanced Manufacturing Efficiency and Product Quality
In addition to size and material customization, advanced technologies and automation can be woven into the production process. For instance, incorporating automated inspection systems into Customized ERW tube mills can enhance the quality control process. With integrated automated quality assurance, manufacturers can detect defects in real-time and make necessary adjustments to minimize scrap and rework. This level of precision and efficiency is vital in industries where product quality can directly impact safety and compliance.
Furthermore, customized ERW tube mill solutions often employ the latest technological innovations such as Industry 4.0 enhancements, including IoT (Internet of Things) capabilities. This allows companies to gather and analyze data from the production line, leading to more informed decision-making and predictive maintenance. By anticipating equipment failures and addressing them proactively, manufacturers can reduce downtime and maintain consistent production levels, which further solidifies their market position.
A lesser-known but critical aspect of customized ERW tube mills is their role in promoting sustainable manufacturing practices. By optimizing production processes and reducing waste through more efficient machinery, companies can significantly lower their environmental footprint. Customized solutions often lead to reduced energy consumption as well, as equipment can run more efficiently based on the specific requirements of production. This alignment with sustainability goals not only appeals to environmentally conscious consumers but can also lead to cost savings through better resource management.
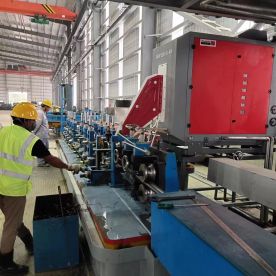
Exploring the Advantages of Customized ERW Tube Mill Solutions for Enhanced Manufacturing Efficiency and Product Quality
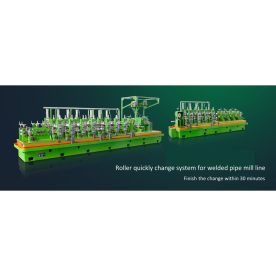