[High frequency welder manufacturer]Choosing the Right High Frequency Welder Manufacturer: Key Considerations for Optimal Performance and Reliability in Industrial Applications
News 2025-1-7
High frequency (HF) welding, also known as dielectric welding, is a crucial process widely employed in various industries such as automotive, textiles, packaging, and electronics. Selecting a high frequency welder manufacturer is a significant decision that can impact your project's efficiency, quality, and overall success. Given the importance of this equipment in modern manufacturing, it is essential to understand the key factors that can influence your choice of a high frequency welder manufacturer.
Understanding High Frequency Welding
High frequency welding involves the use of high-frequency electromagnetic waves to join materials, typically thermoplastics. The process creates localized heating at the interface of the materials, resulting in a strong bond without the need for adhesives or additional materials. This technology is particularly advantageous in several applications, especially for thick materials that require precise control over heat application.
Factors to Consider When Choosing a High Frequency Welder Manufacturer
When looking for a high frequency welder manufacturer, there are several critical aspects that businesses should consider to ensure they make an informed decision:
1. **Experience and Industry Reputation**
An established high frequency welder manufacturer with years of experience in the industry can significantly influence the quality and reliability of the equipment. Researching the manufacturer's background and reading customer reviews can provide insight into their reputation. A manufacturer known for producing high-quality welders and providing excellent customer service can give you peace of mind regarding your investment.
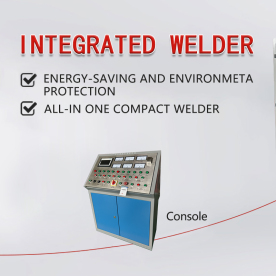
Choosing the Right High Frequency Welder Manufacturer: Key Considerations for Optimal Performance and Reliability in Industrial Applications
The field of welding technology is continually evolving. It's important to choose a manufacturer that stays updated with the latest advancements in high frequency welding equipment. Look for manufacturers that integrate new technologies, such as digital controls, automation, and energy-saving features. These advancements can enhance the efficiency and effectiveness of your welding processes.
3. **Customization Options**
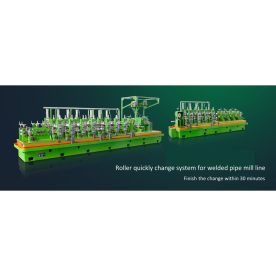
Choosing the Right High Frequency Welder Manufacturer: Key Considerations for Optimal Performance and Reliability in Industrial Applications

Choosing the Right High Frequency Welder Manufacturer: Key Considerations for Optimal Performance and Reliability in Industrial Applications
Investing in high frequency welding equipment also means considering the level of after-sales support provided by the manufacturer. Reliable service and support can make a significant difference in minimizing downtime and ensuring that any issues are resolved quickly. Assess the manufacturer's warranty, availability of spare parts, and the responsiveness of their customer support team.
5. **Capacity and Production Requirements**
Your choice of a high frequency welder manufacturer should also take into account the scale of your operations. Manufacturers often produce welders in various sizes and capacities. Understanding your production volume and the materials involved will help you choose a welder that can meet both your needs and future scalability.
6. **Compliance and Quality Standards**
High frequency welding equipment must comply with industry standards and regulations. Ensure that the manufacturer adheres to stringent quality control measures and possesses certifications that validate their commitment to safety and environmental protection. This aspect can significantly minimize risks associated with using subpar equipment.
7. **Cost Versus Value**
While cost is always an important factor when selecting a high frequency welder manufacturer, it should not be the only deciding aspect. Evaluate the overall value that the equipment brings, including its durability, efficiency, and performance. Sometimes, investing slightly more in a high-quality welder can lead to significant savings over time in terms of maintenance and productivity.
Conclusion
Choosing the right high frequency welder manufacturer is a complex decision that requires careful consideration of various factors, including experience, technology, customization, support services, capacity, compliance, and overall value. Each of these considerations can contribute to your company's operational efficiency and product quality. By investing the time to thoroughly evaluate potential manufacturers, you can ensure that you select a partner that will meet your needs and support your business growth in the competitive landscape of modern manufacturing.