[High frequency welder for metal]Understanding the Advantages and Applications of High Frequency Welders for Metal Fabrication in Various Industries
News 2025-1-6
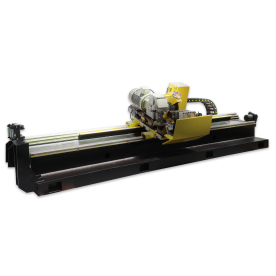
Understanding the Advantages and Applications of High Frequency Welders for Metal Fabrication in Various Industries
What is High Frequency Welding?
High frequency welding utilizes high-frequency electrical currents to generate heat through electromagnetic induction. The process is particularly effective for joining metals and thermoplastics, creating strong, durable, and often seamless welds. By applying heat at specific points, the process minimizes the risk of damaging the surrounding material, which is a significant advantage over traditional welding techniques.
Advantages of High Frequency Welders for Metal
1. **Fast Processing Time**: One of the standout features of high frequency welding is its speed. The process requires only a fraction of the time compared to conventional welding methods. This increased efficiency allows manufacturers to produce more products in a shorter timeframe, enhancing overall productivity.
2. **High-Quality Welds**: High frequency welding produces clean and precise welds, which are often stronger than the base materials being joined. This is particularly important in industries where structural integrity is critical, such as construction and automotive manufacturing.
3. **Minimal Heat-Affected Zone**: Unlike traditional welding methods that can create a large heat-affected zone (HAZ) leading to material warping or weakening, high frequency welding tools create a localized heating effect. This characteristic drastically reduces the risks related to distortion and maintains the material properties around the weld.
4. **Versatile Applications**: High frequency welders for metal can be utilized in a wide array of applications. From joining thin metal sheets to thick materials, the versatility of HF welding makes it ideal for various industries, including aerospace, automotive, electronics, and telecommunications.
5. **Reduced Environmental Impact**: With a growing emphasis on sustainable manufacturing practices, high frequency welding offers an eco-friendlier alternative. The process requires less energy than traditional welding methods, thereby reducing the carbon footprint of the manufacturing process.
Applications of High Frequency Welders
High frequency welders are extensively used in several industries due to their robustness and precision. Here are some notable applications:
1. **Automotive Industry**: HF welding is critical in the automotive sector for producing components like exhaust systems, fuel tanks, and chassis parts. The ability to create strong joints without adding excess weight aligns well with the industry's rigorous standards for safety and performance.
2. **Aerospace Manufacturing**: In the aerospace industry, weight reduction is vital for enhancing fuel efficiency. High frequency welding methods contribute to the production of lightweight, high-strength components, ensuring that these parts meet stringent safety regulations.
3. **Electrical and Electronics Sector**: High frequency welders are employed in the manufacturing of electronic devices, cables, and circuit boards. The precision of the welding process allows manufacturers to make reliable connections without risking damage to sensitive components.
4. **Telecommunications**: HF welding plays a role in the production of equipment such as antennae and transmission lines. Its ability to create robust and high-quality welds is crucial in maintaining signal integrity and durability.
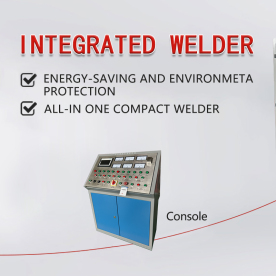
Understanding the Advantages and Applications of High Frequency Welders for Metal Fabrication in Various Industries
Conclusion
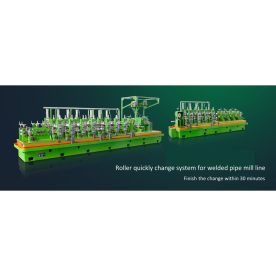