[Solid state HF welder]Exploring the Benefits and Applications of Solid State HF Welder Technology in Modern Manufacturing Processes
News 2025-1-6
In recent years, the industrial landscape has seen a notable evolution in welding technology, particularly with the advent of solid state HF (high frequency) welders. This innovation has revolutionized the way manufacturers approach welding processes, providing enhanced efficiency, precision, and versatility. As industries increasingly seek methods that not only meet production demands but also prioritize sustainability and energy efficiency, solid state HF welders are becoming an indispensable tool in welding applications across various sectors.
Understanding Solid State HF Welding Technology
Solid state HF welding is a process that utilizes semiconductor technology to generate high-frequency electrical energy, facilitating the welding of thermoplastic materials and thin metals. Unlike traditional welding methods, which often rely on vacuum tubes or transformers to produce high-frequency signals, solid state HF welders employ solid-state devices such as transistors. This results in several advantages: improved performance, smaller equipment footprint, lower energy consumption, and increased reliability.
The principle behind solid state HF welding is the induction of heat through high-frequency electromagnetic fields. When an electrical current passes through the electrodes, a magnetic field is generated, which induces heat in the materials being welded. This process allows for rapid and efficient melting, enabling operators to achieve strong, high-quality welds with minimal material distortion. As such, solid state HF welders are particularly well-suited for applications that require precise control over the welding process.
Key Benefits of Solid State HF Welders
1. **Energy Efficiency**: One of the most significant advantages of solid state HF welders is their energy efficiency. These machines consume less power compared to traditional welders, which often waste energy in the form of heat loss during operation. The compact design and operational efficiency of solid state HF welders lead to significant cost savings in energy consumption over time.
2. **Reduced Maintenance**: Solid state HF welders have fewer moving parts compared to traditional systems, resulting in lower maintenance requirements. The reliance on solid-state components minimizes the likelihood of mechanical failures, thus reducing downtime and maintenance costs. Manufacturers can benefit from more consistent production schedules and lower operational expenses.
3. **Improved Weld Quality**: The level of precision offered by solid state HF welders allows for superior weld quality. The controlled heating enables operators to minimize the potential for overheating or underheating, which can compromise weld integrity. This results in stronger, more durable welds, particularly when working with advanced materials.
4. **Versatile Applications**: Solid state HF welding technology is versatile and can be used across a wide range of industries, including automotive, aerospace, electronics, and packaging. Whether it is joining thermoplastic components or welding thin gauge metals, the adaptability of this technology makes it an invaluable asset in modern manufacturing.
5. **Compact Design**: The compact design of solid state HF welders allows for flexible installation options in workshop settings. They can fit into tight spaces and can easily be integrated into existing production lines without requiring significant modifications. This adaptability is particularly important for manufacturers looking to optimize their production environments.
Applications of Solid State HF Welding
1. **Medical Device Manufacturing**: In the medical field, precision is paramount. The solid state HF welding process is utilized to join components of medical devices, ensuring hermetic seals and maintaining sterility. Its capability to work with a variety of plastics is particularly beneficial in producing medical packaging.
2. **Automotive Industry**: The automotive sector relies heavily on solid state HF welding for assembling components such as fuel tanks, bumpers, and interior trim. The ability to achieve strong, aesthetically pleasing joints is critical in automotive applications, and solid state HF welders excel in this respect.
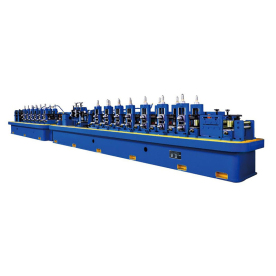
Exploring the Benefits and Applications of Solid State HF Welder Technology in Modern Manufacturing Processes
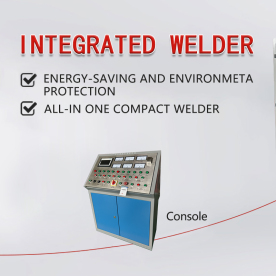
Exploring the Benefits and Applications of Solid State HF Welder Technology in Modern Manufacturing Processes
4. **Electrical Components**: In electronics manufacturing, solid state HF welders are used to create connections in circuit boards and other components, where reliability and precision are vital.
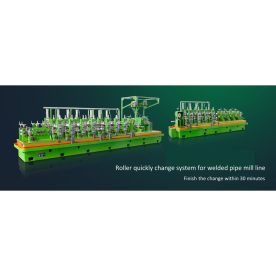
Exploring the Benefits and Applications of Solid State HF Welder Technology in Modern Manufacturing Processes
The solid state HF welder represents a significant advancement in welding technology that aligns with the evolving needs of modern manufacturing. With benefits such as energy efficiency, reduced maintenance, improved weld quality, and versatility, it is no wonder that businesses are increasingly adopting this technology. As industries continue to push for innovations that enhance productivity and sustainability, solid state HF welders are set to play a crucial role in shaping the future of manufacturing processes.