[Mould for tube mill]Understanding the Importance of Mould for Tube Mill: Enhancing Precision and Efficiency in Tube Manufacturing
News 2025-1-6
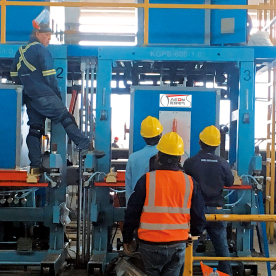
Understanding the Importance of Mould for Tube Mill: Enhancing Precision and Efficiency in Tube Manufacturing
In the ever-evolving world of manufacturing, particularly in the tube and pipe industry, the choice of materials and machinery can significantly impact the product quality and operational efficiency. A critical component in the production of tubes and pipes is the mould for tube mills. With its pivotal role in ensuring precision, durability, and productivity, understanding the significance of this component is essential for manufacturers who seek to optimize their operations.
What is a Mould for Tube Mill?
A mould for a tube mill is a crucial part of the manufacturing process used to form and shape metal into tubes or pipes. It acts as the primary shaping mechanism through which molten or semi-molten metal is drawn to create the desired tube dimensions. The process typically involves feeding a flat strip of metal into a series of rollers, which, guided by the mould, continuously shape the material into its final tubular form.
Moulds can be made from various materials, including steel, carbide, and other alloys, depending on the requirements of the manufacturing process and the type of tube being produced. Their design may vary significantly depending on the specifications needed for the inner and outer diameters of the tubes and other structural characteristics.
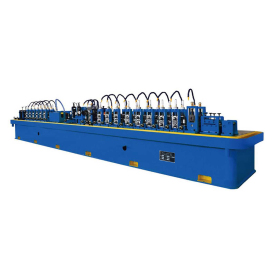
Understanding the Importance of Mould for Tube Mill: Enhancing Precision and Efficiency in Tube Manufacturing
1. **Precision Engineering**
Moulds are designed with precision to ensure that the tubes produced meet strict dimensional tolerances. A high-quality mould minimizes the variability in tube dimensions, which is crucial for industries that require exact specifications—such as automotive, aerospace, and construction. The precision of the mould directly affects the quality of the finished product, which can lead to reduced scrap rates and improved overall efficiency.
2. **Improved Production Speed**
Efficiency is vital in tube mill operations, as manufacturers strive to produce high volumes in shorter timeframes. Well-engineered moulds allow for quicker production cycles by facilitating smoother material flow and quicker handling of the tubes. This speed ultimately translates into higher throughput and reduced production costs, enhancing profit margins.

Understanding the Importance of Mould for Tube Mill: Enhancing Precision and Efficiency in Tube Manufacturing
One of the most notable advantages of modern moulds for tube mills is their versatility. Manufacturers can produce tubes of various shapes and sizes using adaptable mould designs. This flexibility allows companies to meet diverse customer demands without needing to invest in different manufacturing setups for each product type. It’s particularly beneficial in an era where customization and specialized products are increasingly in demand.
Material Selection and Maintenance
Choosing the right material for the mould is crucial, as it needs to withstand significant wear and tear due to constant mechanical contact and heat generation during the manufacturing process. High-quality steel and carbide are popular choices due to their durability and thermal resistance. Regular maintenance and inspections of the mould are also essential practices to ensure a consistent product quality and to prolong the lifespan of the mould itself.
Routine maintenance may include checking for wear, making necessary adjustments, and adhering to scheduled cleanings to prevent any build-up that could affect overall performance. Investing in training for operators on how to properly care for and manage the moulds can also lead to longer service life and optimal performance.
The Future of Tube Mill Moulds
As technology continues to advance, the future of moulds for tube mills is promising. Innovations such as 3D printing are beginning to find their way into the production of moulds, allowing for rapid prototyping and the creation of complex geometries that were previously difficult or impossible to achieve. Additionally, the integration of smart technologies, such as sensors that monitor wear and production efficiency, is transforming the traditional tube mill operations into more intelligent, data-driven processes.
Conclusion
The mould for tube mills plays an indispensable role in the efficiency and precision of tube manufacturing. By understanding its importance and investing in high-quality designs, materials, and maintenance practices, manufacturers can enhance their operations and product output. As the industry continues to innovate, staying abreast of the latest developments in mould technology will be crucial for manufacturers looking to maintain a competitive edge in the market. Ultimately, the mould is not just a tool in the manufacturing process; it is a cornerstone of quality and efficiency in tube production.