[Precision Solid state HF welder]Advancements in Welding Technology: The Impact of Precision Solid State HF Welder on Modern Manufacturing Processes
News 2025-1-6
In recent years, the landscape of welding technology has transformed markedly, driven by continuous innovations in engineering and materials science. Among these advancements, the Precision Solid State HF (High Frequency) Welder stands out as a significant breakthrough that has revolutionized a range of manufacturing processes. This cutting-edge technology not only improves efficiency but also enhances the quality and reliability of welded products across diverse industries such as automotive, aerospace, and electronics.
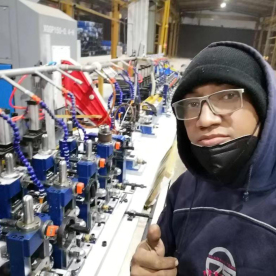
Advancements in Welding Technology: The Impact of Precision Solid State HF Welder on Modern Manufacturing Processes
One of the standout features of the Precision Solid State HF Welder is its ability to generate controlled heat, ensuring that only the weld area is affected. This characteristic is crucial for maintaining the integrity of the surrounding materials, which is especially vital in industries where safety and durability are paramount. For instance, in aerospace applications, where components must endure extreme conditions, the consistency and reliability of the weld are critical.
Moreover, the technology behind solid-state HF welding has significantly improved over the past few decades. Early HF welders relied on vacuum tubes, which were less energy-efficient and required more maintenance. The shift to solid-state technology means improved energy efficiency, a smaller machine footprint, and greater reliability. Modern precision welders utilize advanced electronic components that enable precise control of frequency, power, and timing. This automation not only enhances welding precision but also allows for greater customization according to specific project requirements.
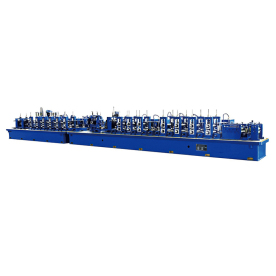
Advancements in Welding Technology: The Impact of Precision Solid State HF Welder on Modern Manufacturing Processes
Another important aspect of using the Precision Solid State HF Welder is its environmental impact. Traditional welding processes, often characterized by significant heat and smoke emissions, can lead to harmful environmental effects. In contrast, solid-state HF welding is a cleaner technology that generates minimal waste and fewer emissions. The reduction in heat generation also leads to lower energy consumption, contributing to a more sustainable manufacturing process.
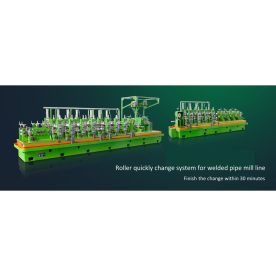
Advancements in Welding Technology: The Impact of Precision Solid State HF Welder on Modern Manufacturing Processes
Despite its many advantages, the adoption of the Precision Solid State HF Welder does come with its set of challenges. For instance, the initial investment can be higher than for traditional welding equipment, which may deter some companies from making the switch. Additionally, the technology necessitates skilled operators who can fully exploit its capabilities and manage the complexity of sophisticated control systems.
Nevertheless, the long-term benefits—higher quality welds, increased production efficiencies, reduced operational costs, and a smaller environmental footprint—tend to outweigh the initial hurdles. As industries continue to evolve and demand more advanced solutions, the Precision Solid State HF Welder will likely play a pivotal role in the next generation of manufacturing processes.
In conclusion, the Precision Solid State HF Welder represents a significant advancement in welding technology, offering numerous advantages that are increasingly relevant in modern manufacturing. Its combination of efficiency, precision, and versatility makes it a valuable asset across various industries, paving the way for higher quality products and streamlined production processes. As this technology continues to develop, it undoubtedly holds the potential to reshape the welding landscape and drive further innovations in manufacturing.