[High frequency welder for metal]Understanding the Benefits and Applications of High Frequency Welder for Metal in Modern Manufacturing Processes
News 2025-1-4
****In the world of metalworking, welding technology has evolved significantly over the years, leading to the development of advanced methods that improve efficiency, precision, and quality. Among these technologies, high frequency welding has emerged as a powerful technique used in various industries for joining metal components. This article delves into the essentials of high frequency welders, exploring their benefits, applications, and how they fit into modern manufacturing processes.
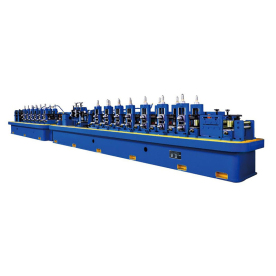
Understanding the Benefits and Applications of High Frequency Welder for Metal in Modern Manufacturing Processes
High frequency welding, also known as high-frequency electromagnetic welding or induction welding, is a process that utilizes high-frequency electromagnetic fields to heat metals to a point where they can be joined without the need for filler materials. This technique is particularly effective for welding thin-walled materials, such as tubes and pipes, and is widely used across several industries including automotive, aerospace, and HVAC.
The Process
The high frequency welding process begins by positioning two metal pieces in close proximity. An induction coil generates a high-frequency electromagnetic field that induces eddy currents in the metal. The resistance caused by these currents generates heat at the surface of the metal workpieces. As the metals reach the desired temperature, the edges become plastic and are pressed together, creating a seamless weld.
Advantages of High Frequency Welding
1. **Speed and Efficiency**: One of the most significant advantages of high frequency welding is its speed. The process allows for rapid heating and cooling, resulting in shorter cycle times compared to conventional welding methods. This increased efficiency translates to higher throughput in manufacturing plants.
2. **Quality and Consistency**: High frequency welding produces strong and consistent welds with minimal distortion. The controlled heat input ensures that the welded areas maintain their desired mechanical properties, leading to less post-weld treatment and inspection.
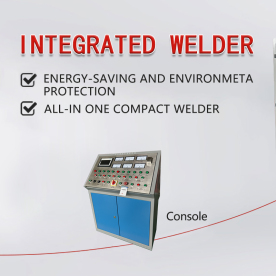
Understanding the Benefits and Applications of High Frequency Welder for Metal in Modern Manufacturing Processes
4. **Versatility**: High frequency welders can be used to join a variety of metals, including steel, stainless steel, and aluminum, making them versatile tools in the manufacturing process. Moreover, they are capable of handling a range of thicknesses, which broadens their application scope.
5. **Improved Safety**: The high frequency welding process does not generate harmful fumes or smoke typically associated with traditional arc welding. Additionally, since no open flames are involved, the risk of fire hazards is significantly lower.

Understanding the Benefits and Applications of High Frequency Welder for Metal in Modern Manufacturing Processes
1. **Automotive Industry**: High frequency welders are extensively used in the automotive industry for manufacturing exhaust systems, fuel tanks, and other critical components. The ability to produce strong and lightweight structures makes this technique ideal for the automotive sector, where efficiency and performance are paramount.
2. **Aerospace Manufacturing**: In the aerospace industry, high frequency welders contribute to producing lightweight and durable materials. The aerospace sector demands high precision and quality, which can be achieved through expert use of high frequency welding techniques.
3. **HVAC Systems**: High frequency welding is vital in the HVAC industry for fabricating components such as heat exchangers, pipes, and ducts. The ability to create strong and leak-proof joints is crucial for the efficient operation of HVAC systems.
4. **Construction and Infrastructure**: In construction, high frequency welding is employed for fabricating steel structures, reinforcing bars, and piping systems. This technique enhances the strength and durability of jointed components, which is essential for safe infrastructure development.
Conclusion
The high frequency welder for metal stands out as a revolutionary approach to welding technology, offering numerous advantages that meet the demands of modern manufacturing. With its speed, efficiency, and ability to produce high-quality welds, it is becoming an integral tool across various industries. As manufacturers continue to seek innovative ways to improve their processes, the role of high frequency welding will likely expand, cementing its place within the future of metal fabrication. Embracing this technology can significantly enhance production capabilities, reduce costs, and ultimately lead to more robust and reliable products.