[IF pipe seam annealing machine ]Exploring the Innovation in Pipe Seam Annealing Machines: Enhancing Efficiency and Quality in Metalworking Industries
News 2025-1-3
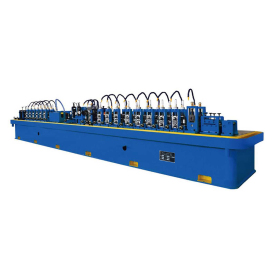
Exploring the Innovation in Pipe Seam Annealing Machines: Enhancing Efficiency and Quality in Metalworking Industries
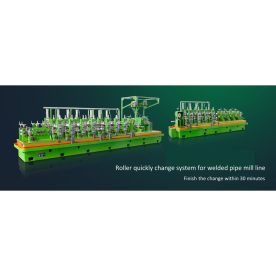
Exploring the Innovation in Pipe Seam Annealing Machines: Enhancing Efficiency and Quality in Metalworking Industries
The fundamental operation of the IF pipe seam annealing machine involves the use of high-frequency induction heating. This method generates heat directly within the metal, reducing the energy loss associated with traditional heating methods, such as furnaces or resistive heating. The result is an efficient process that significantly speeds up production while ensuring a consistent temperature profile along the seam of the pipe. This precision is vital, as it allows the material to recover from the stresses induced during welding, leading to a more uniform and stronger weld.
One of the most notable advantages of using an IF pipe seam annealing machine is the reduction in overall production time. Traditional methods often require longer heating times, leading to bottlenecks in the manufacturing process. In contrast, the induction heating technology allows for rapid heating and cooling cycles. This efficiency translates into higher throughput and the ability to meet the growing demands of various industries without compromising on quality.
Moreover, the use of an IF pipe seam annealing machine can lead to significant energy savings. By directly heating the metal, there is less waste heat generated compared to traditional methods. Energy consumption is minimized, contributing to a more sustainable manufacturing process. As the global focus shifts towards sustainability and reducing carbon footprints, the adoption of energy-efficient technologies like the IF pipe seam annealing machine becomes increasingly important.
The process also has a profound impact on product quality. The induction heating method leads to a more uniform temperature distribution, which is crucial for achieving optimal mechanical properties. The controlled heating and subsequent cooling eliminate the risk of overheating and overheating zones, which can lead to brittleness in the weld. As a result, manufacturers can produce pipes with reliable and consistent mechanical properties, enhancing their market competitiveness.

Exploring the Innovation in Pipe Seam Annealing Machines: Enhancing Efficiency and Quality in Metalworking Industries
Furthermore, the versatility of IF pipe seam annealing machines cannot be understated. These machines can be adapted to accommodate various pipe sizes and materials, making them suitable for a wide range of applications. From small-diameter pipes used in residential plumbing to large-diameter industrial pipes, the IF pipe seam annealing machine offers flexibility that is appealing to manufacturers looking to diversify their product offerings.
In conclusion, the IF pipe seam annealing machine stands at the forefront of modern metalworking technology. With its advanced induction heating system, it not only enhances the manufacturing efficiency of welded pipes but also improves the quality and safety of the end products. As industries continue to evolve, the embrace of innovative solutions like the IF pipe seam annealing machine will be crucial in meeting the demands of an ever-changing market. Manufacturers that invest in such technologies position themselves to succeed in a competitive landscape, ultimately leading to greater productivity, sustainability, and quality assurance in their operations.