[High frequency welder for plastic]Unlocking the Future of Plastic Manufacturing: The Innovative Role of High Frequency Welder for Plastic in Industrial Applications
News 2025-1-3
In today’s fast-paced industrial landscape, the need for efficient, reliable, and high-quality manufacturing techniques has never been greater. Among the various methods employed in the production of plastic components, high frequency welding has emerged as a transformative technology. The high frequency welder for plastic is increasingly becoming crucial in a range of industries, including automotive, medical, and consumer goods. This article delves into the importance, functioning, and advantages of utilizing high frequency welding for plastic applications.
Understanding High Frequency Welding
High frequency welding, also referred to as RF welding (Radio Frequency welding) or dielectric welding, is a sophisticated method that uses high-frequency electromagnetic energy to join plastic materials. The process is particularly effective for thermoplastic materials, which can be melted and fused together under the right conditions. The technology is widely used to create strong, permanent seams in various plastic components, making it an integral part of modern manufacturing processes.
The mechanism behind high frequency welding involves applying high-frequency electromagnetic waves to the overlapping surfaces of the plastic materials. This action generates heat within the material, causing it to melt and bond together. After a set duration, the machine stops generating waves, allowing the materials to cool and form a solid bond. This welding process can be adjusted to accommodate different material thicknesses and types, providing versatility in production.
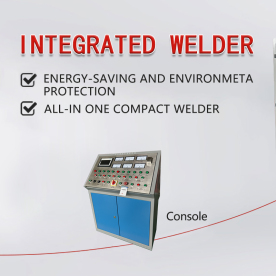
Unlocking the Future of Plastic Manufacturing: The Innovative Role of High Frequency Welder for Plastic in Industrial Applications
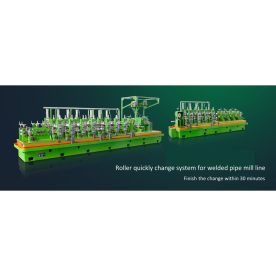
Unlocking the Future of Plastic Manufacturing: The Innovative Role of High Frequency Welder for Plastic in Industrial Applications
The high frequency welder for plastic is utilized in various sectors due to its effectiveness and efficiency. In the **automotive industry**, parts such as air ducts, fuel tanks, and interior components are often manufactured using this welding technology. The ability to create lightweight, strong, and leak-proof components is essential for automotive applications.
The **medical field** also benefits significantly from high frequency welding. Many medical disposables, such as sterile bags, pouches, and tubing, require precise sealing to maintain sterility and prevent contamination. High frequency welding ensures that these products are produced quickly and reliably, meeting stringent industry standards.
In the **consumer goods sector**, the production of items like inflatable products, tarpaulins, and various packaging materials relies on the capabilities of high frequency welding. The process allows manufacturers to produce large volumes of products that are not only durable but also aesthetically pleasing.
Advantages of High Frequency Welding
1. **Speed and Efficiency**: High frequency welding allows for rapid production cycles, which can significantly increase output rates. The process’s ability to weld multiple layers simultaneously also contributes to overall efficiency.
2. **Strong Bonds**: The welds created using high frequency technology are exceptionally strong, ensuring durable and long-lasting products. This characteristic is particularly important in applications where the integrity of the weld is critical.
3. **Versatility**: This method can be used to bond a wide variety of thermoplastic materials, including PVC, polyurethane, and PET. This versatility makes it suitable for a range of applications across multiple industries.
4. **Clean Process**: High frequency welding is a solvent-free process, meaning it does not require any adhesives or harmful chemicals. This aspect not only makes it environmentally friendly but also reduces the risk of contamination in medical and food applications.

Unlocking the Future of Plastic Manufacturing: The Innovative Role of High Frequency Welder for Plastic in Industrial Applications
Conclusion
In conclusion, the high frequency welder for plastic stands out as a pivotal technology in contemporary manufacturing. Its ability to create strong, efficient, and reliable bonds makes it a preferred choice in industries such as automotive, medical, and consumer goods. As the demand for high-quality plastic components continues to grow, so will the importance of high frequency welding as a feasible solution for manufacturers looking to innovate and enhance their production processes. By investing in this technology, businesses can ensure they stay competitive and meet consumer expectations in a rapidly evolving marketplace.