[Precision ERW tube mill machinery]The Evolution and Impact of Precision ERW Tube Mill Machinery in Modern Manufacturing: A Comprehensive Overview
News 2025-1-3
In the modern manufacturing landscape, Precision Electric Resistance Welded (ERW) tube mill machinery has emerged as a critical player in producing high-quality tubular products. This specialized machinery has not only revolutionized the way steel tubes are manufactured but also enhanced the efficiency and quality of various industries, including construction, automotive, and energy. In this article, we will delve into the evolution, functionality, advantages, and future prospects of precision ERW tube mill machinery.
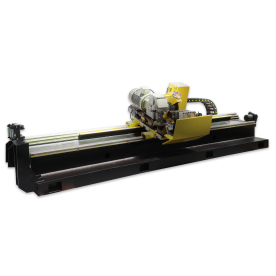
The Evolution and Impact of Precision ERW Tube Mill Machinery in Modern Manufacturing: A Comprehensive Overview
The concept of electric resistance welding dates back to the early 19th century, but it wasn't until the mid-20th century that the technology advanced significantly. The introduction of electricity and automation allowed for the creation of sophisticated machinery capable of producing seamless and precision tubes. Initial ERW tube mill machinery was bulky and less efficient, often resulting in variations in product quality. However, with advancements in technology and materials science, modern precision ERW tube mills have become remarkably efficient, producing tubes that meet stringent quality standards.
Functionality of Precision ERW Tube Mill Machinery
Precision ERW tube mill machinery operates through a series of well-coordinated roller stations that form and weld flat steel strips into tubular shapes. The process starts with the feeding of a flat coil of steel, which is then shaped into a tube by driven rolls. Electric resistance welding is used to join the edges of the strip. Here’s a breakdown of the steps involved:
1. **Material Preparation**: The process begins with high-quality flat steel strips being fed into the machine. Manufacturers often use various grades of steel depending on the end application.
2. **Forming Rolls**: The flat strip passes through a series of forming rolls, which gradually shape it into a tubular configuration.
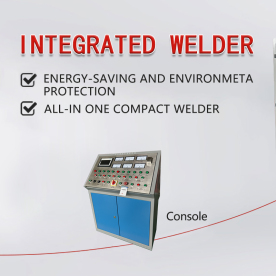
The Evolution and Impact of Precision ERW Tube Mill Machinery in Modern Manufacturing: A Comprehensive Overview
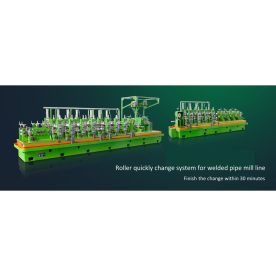
The Evolution and Impact of Precision ERW Tube Mill Machinery in Modern Manufacturing: A Comprehensive Overview
5. **Finishing Operations**: The final steps may include cutting the tube to length, surface finishing, and inspection to meet quality standards.
Advantages of Precision ERW Tube Mill Machinery
One of the primary advantages of precision ERW tube mills is their ability to produce a wide range of tube sizes and specifications. This flexibility is crucial in industries where varying dimensions and properties are required. Other notable benefits include:
- **High Efficiency**: Modern machinery is equipped with automation and advanced control systems, enabling continuous production with minimal downtime.
- **Cost-Effectiveness**: The ERW process produces less waste compared to traditional methods, which significantly reduces manufacturing costs.
- **Quality Control**: Precision ERW machinery incorporates advanced sensors and monitoring systems to ensure consistent quality throughout the production process.
- **Versatile Applications**: ERW tubes are widely used in various sectors—ranging from structural applications in construction to intricate components in automotive and mechanical engineering.
- **Sustainability**: The efficiency of the ERW process results in lower energy consumption and waste, making it a more environmentally friendly option compared to alternatives.
Future Prospects of Precision ERW Tube Mill Machinery
The future of precision ERW tube mill machinery looks promising with ongoing advancements in technology, such as Industry 4.0 and smart manufacturing. These innovations will likely bring about enhanced automation solutions, predictive maintenance, and better data analytics, allowing for further improvements in efficiency and product quality. Additionally, as global markets push for greener manufacturing processes, the ERW method may gain further significance due to its lower environmental impact.
In conclusion, precision ERW tube mill machinery has become a cornerstone of modern manufacturing, offering a plethora of advantages that enhance productivity and quality. As the demand for high-performance tubular products continues to grow, the evolution of this technology will play a crucial role in shaping the future of various industries. Embracing these advancements will not only benefit manufacturers but also contribute to more sustainable practices in the industry at large.