[Automatic Tube making machine]Revolutionizing Packaging: The Advantages and Features of Automatic Tube Making Machines in Modern Manufacturing
News 2025-1-1
****In today’s fast-paced manufacturing environment, efficiency and precision are paramount. Industries ranging from cosmetics to pharmaceuticals require packaging solutions that not only preserve product quality but also enhance branding. This has led to the rise of automatic tube making machines, which have become indispensable in the production line of various products. These machines are designed to produce high-quality tubes at a rapid pace, offering immense advantages over traditional methods of tube manufacturing.
The Basics of Automatic Tube Making Machines
Automatic tube making machines are advanced pieces of equipment that automate the entire process of tube production, from material feeding to the sealing and cutting of finished products. These machines are capable of producing different types of tubes, such as round, oval, or even custom-shaped tubes, using materials like plastic, aluminum, and laminate. By integrating various technologies, these machines ensure that the manufacturing process is not only fast but also consistent in quality.
Key Features that Enhance Efficiency
One of the most significant advantages of automatic tube making machines is their ability to operate with minimal human intervention. This not only reduces labor costs but also minimizes the risk of human error. Features such as automatic material feeding, precise control systems, and integrated quality checks help maintain a high level of accuracy throughout the production process.
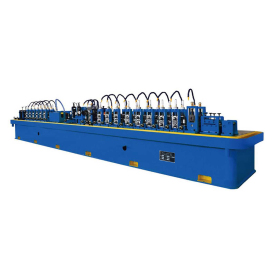
Revolutionizing Packaging: The Advantages and Features of Automatic Tube Making Machines in Modern Manufacturing
Versatility Across Industries
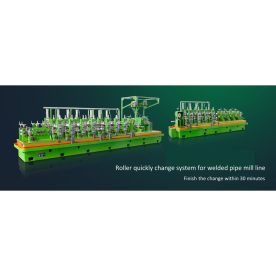
Revolutionizing Packaging: The Advantages and Features of Automatic Tube Making Machines in Modern Manufacturing
Environmental Sustainability
With growing concerns about environmental sustainability, manufacturers are under increasing pressure to adopt more eco-friendly practices. Automatic tube making machines often feature options for producing tubes with reduced material usage and options for recycling. Advanced models can operate with biodegradable materials, aligning packaging production with global sustainability initiatives. This not only helps companies meet regulatory requirements but also appeals to environmentally conscious consumers.
Cost-Effectiveness in Production
While the initial investment in an automatic tube making machine may seem significant, the long-term savings are substantial. These machines significantly reduce the cost per unit by increasing production speeds and reducing waste. Moreover, the durability of automatic machines ensures lower maintenance costs over time. As the production rates increase, businesses can achieve economies of scale, ultimately leading to higher profit margins.
Quality Assurance and Consistency
Quality is non-negotiable in manufacturing; consumers expect perfect products every time. Automated tube production allows for stringent quality control measures, ensuring that each tube produced meets stringent industry standards. Features such as sensors that detect imperfections and ensure proper sealing are integral to maintaining this level of quality.
Conclusion
