[Sharp HSS Blade for Machining Applications]Maximizing Efficiency and Precision in Machining Applications with Sharp HSS Blade Technology
News 2025-1-1
In the manufacturing and machining industry, efficiency, precision, and tool longevity are paramount. Among the various tools available to machinists, the sharp High-Speed Steel (HSS) blade stands out as a critical component for various machining applications. Advances in coatings, geometries, and manufacturing processes have enhanced the performance of HSS blades, aligning their capabilities with the evolving demands of modern machining tasks.
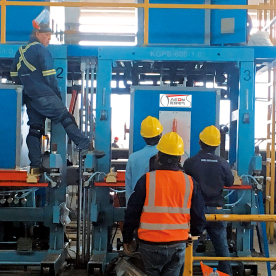
Maximizing Efficiency and Precision in Machining Applications with Sharp HSS Blade Technology
One of the main advantages of a sharp HSS Blade for machining applications is its ability to maintain cutting efficiency. A sharp edge minimizes the amount of force required to cut through materials, which not only enhances the quality of the finished product but also increases the overall speed of the machining process. This efficiency translates into reduced cycle times and increased productivity, essential factors in today’s competitive manufacturing landscape.
In turning applications, sharp HSS blades can significantly impact surface finish and dimensional accuracy. When the blade is well-maintained and sharp, it creates a smoother cutting action that reduces the potential for defects such as chatter or tool vibration. This improved surface finish can eliminate the need for additional finishing processes and reduces material wastage, making the overall machining practice more cost-effective. Furthermore, sharp blades contribute to maintaining tight tolerances, which is critical in sectors such as aerospace and automotive, where specifications are stringent.
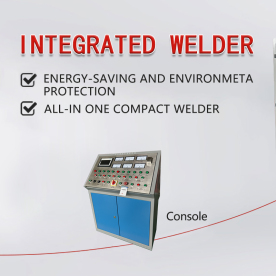
Maximizing Efficiency and Precision in Machining Applications with Sharp HSS Blade Technology
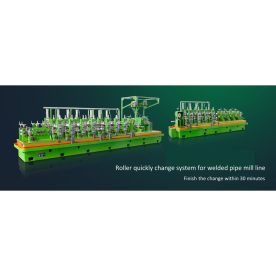
Maximizing Efficiency and Precision in Machining Applications with Sharp HSS Blade Technology
Moreover, the cost-effectiveness of using sharp HSS blades should not be overlooked. While these blades may require an investment upfront, their durability and efficiency can result in substantial savings over time. Regular maintenance, including sharpening and appropriate storage, can extend the life of the blades, further enhancing their cost-efficiency. In large-scale machining operations, this aspect translates into lower tool replacement rates and a decrease in overall operational costs.
Finally, investing in high-quality sharp HSS blades paired with proper machining techniques is essential for generating optimal results. Operators should essentially adhere to recommended cutting parameters and regularly monitor tool wear to ensure consistent quality. Training and education on the appropriate use and maintenance of sharp HSS blades can elevate a machining operation’s performance and precision.
In conclusion, the role of sharp HSS blades in machining applications cannot be overstated. Their unique properties and advantages make them indispensable tools in the manufacturing industry. By ensuring that these blades are kept sharp and well-maintained, machinists can maximize efficiency, achieve superior surface finishes, and minimize operational costs, paving the way for success in an increasingly competitive market. To leverage the full potential of machining operations, investing time and resources in sharp HSS blade technology is paramount.