[Solid state HF welder customization service]Transform Your Manufacturing Process with Tailored Solid State HF Welder Customization Service for Enhanced Efficiency and Performance
News 2025-1-1
**Title: **In today's fast-paced manufacturing environment, companies are constantly seeking ways to improve efficiency and product quality. One innovative solution that has gained traction is the customization of solid state high-frequency (HF) welders. By investing in tailored solid state HF welder customization services, businesses can significantly enhance their operational capabilities, reduce production costs, and improve overall output quality.
Understanding Solid State HF Welding
Solid state HF welding, a sophisticated joining process, uses high-frequency electromagnetic energy to weld materials, primarily metals and thermoplastics. The technology harnesses heat generated from electrical resistance to create strong bonds, making it ideal for various applications, including automotive, aerospace, and electronics manufacturing. With precise control over the welding parameters, solid state HF welding minimizes distortion and maintains material integrity, which is crucial for producing high-quality components.
Despite the efficiency of standard HF welders, many manufacturers face challenges in adapting their machines to specific production needs. This is where solid state HF welder customization services come into play.
Why Customization is Key
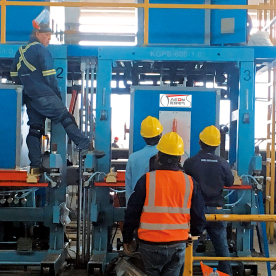
Transform Your Manufacturing Process with Tailored Solid State HF Welder Customization Service for Enhanced Efficiency and Performance
2. **Enhanced Flexibility and Control**: Custom solid state HF welders provide greater flexibility in terms of parameter settings. This allows manufacturers to adjust power levels, frequency, and welding time, ensuring optimal results for diverse applications. With better control over the welding process, companies can achieve tighter tolerances and consistently high-quality welds.
3. **Integration with Existing Systems**: A properly customized HF welder can be designed to integrate seamlessly with existing machinery and automation systems. This reduces downtime during transition periods, minimizes the need for retraining staff, and allows for smoother workflow continuity.
4. **Scalability for Future Needs**: As businesses grow and evolve, their production needs can change. By opting for a customization service, manufacturers can design their HF welders to be scalable, allowing for upgrades and modifications without complete equipment overhauls. This future-proofs the investment and supports long-term operational goals.
The Customization Process
The solid state HF welder customization process typically involves several key steps:
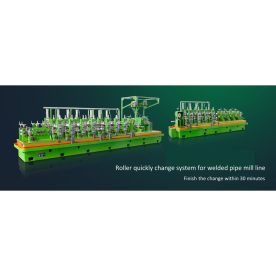
Transform Your Manufacturing Process with Tailored Solid State HF Welder Customization Service for Enhanced Efficiency and Performance

Transform Your Manufacturing Process with Tailored Solid State HF Welder Customization Service for Enhanced Efficiency and Performance
- **Prototyping and Testing**: Before full-scale production, a prototype of the customized welder may be created for rigorous testing. This step is crucial for identifying any potential issues and fine-tuning the machine's performance.
- **Implementation and Training**: Once the customization is completed and tested, the new solid state HF welder is integrated into the production line. Training sessions are conducted for operators to ensure they are adept at using the new features and functionalities of the machine.
- **Ongoing Support and Maintenance**: Customization doesn't end with installation. Many service providers offer ongoing support and maintenance services to address any operational challenges and keep the equipment running smoothly.
Conclusion
Investing in a solid state HF welder customization service can be a game changer for manufacturers looking to enhance efficiency, quality, and adaptability in their production processes. With tailored solutions that address specific needs, manufacturers can overcome challenges, improve their competitive edge, and stay ahead in a demanding marketplace. As the field of manufacturing continues to evolve, embracing customization is no longer a luxury, but a necessity for success.