[All-in-one High Frequency Welder for Metal Processing]Revolutionizing Metal Fabrication with the All-in-One High Frequency Welder for Metal Processing: A Comprehensive Overview
News 2024-12-31
The world of metal processing is continually evolving, with advancements in technology that promise to enhance efficiency, precision, and versatility in manufacturing. One such innovation making waves in this sector is the All-in-One High Frequency Welder for Metal Processing. This state-of-the-art equipment is engineered to meet the diverse needs of metal fabricators, offering a seamless solution that combines different welding techniques in one versatile machine. In this article, we will delve into the features, benefits, and applications of high frequency welders, shedding light on why they are a game changer for the industry.
Understanding High Frequency Welding
High frequency welding is a method that utilizes high frequency electromagnetic fields to join materials, predominantly metals, through the induction of heat. This technique is particularly favored for its ability to produce strong and precise welds while minimizing distortion, making it an ideal choice for manufacturing applications that require high tolerances and superior finish quality. Traditionally, metal processing equipment required separate machines for various welding processes. However, the advent of All-in-One high frequency welders has transformed this paradigm, offering a compact and efficient alternative.
Features of the All-in-One High Frequency Welder
The All-in-One High Frequency Welder is equipped with a range of features designed to enhance its usability and performance:
1. **Multi-Functionality**: As the name suggests, this welder combines several welding processes, including induction, resistance, and TIG welding. Such versatility allows for handling different projects without the need for multiple machines.
2. **Intelligent Control Systems**: Most modern high frequency welders come with advanced control panels that allow users to adjust parameters easily. With programmable settings, operators can achieve consistent results by maintaining the desired welding temperature and pressure.
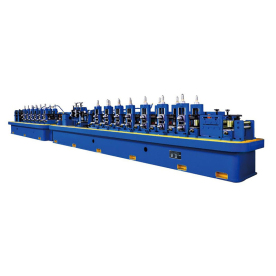
Revolutionizing Metal Fabrication with the All-in-One High Frequency Welder for Metal Processing: A Comprehensive Overview
4. **High Efficiency**: These welders are designed to be energy-efficient, often incorporating features that reduce power consumption while delivering high-quality welds. This not only lowers operating costs but also contributes to sustainable manufacturing practices.
5. **Enhanced Safety Features**: High frequency welders are equipped with safety mechanisms such as automatic shut-off systems, overcurrent protection, and thermal sensors that monitor the machine's operating temperature, ensuring safe use in industrial settings.
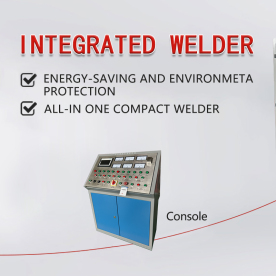
Revolutionizing Metal Fabrication with the All-in-One High Frequency Welder for Metal Processing: A Comprehensive Overview
Implementing an All-in-One High Frequency Welder in metal processing operations offers numerous advantages:
1. **Cost-Effectiveness**: With multiple welding functions integrated into a single machine, companies can save on both equipment costs and maintenance expenses. The ability to perform various welding tasks means that businesses can optimize their investment and limit downtime.
2. **Increased Productivity**: The fast welding speeds and efficient operations of high frequency welders enable manufacturers to boost their production rates. Faster welding processes mean quicker turnaround times for projects, allowing businesses to meet customer demands more effectively.
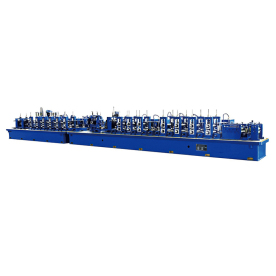
Revolutionizing Metal Fabrication with the All-in-One High Frequency Welder for Metal Processing: A Comprehensive Overview
4. **Flexibility in Applications**: The versatility of All-in-One welders makes them suitable for a wide range of applications, from automotive and aerospace to construction and art fabrication. This flexibility allows businesses to diversify their service offerings and adapt to changing market demands.
5. **Simplified Training**: Having a single machine with multiple functions simplifies operator training and reduces the learning curve. Workers can become proficient in utilizing one piece of equipment, which is particularly beneficial for businesses with limited manpower.
Applications in Metal Processing
The All-in-One High Frequency Welder is applicable in numerous industries, including:
- **Automotive Industry**: Used for components such as exhaust systems and chassis parts. - **Aerospace Sector**: Ideal for fabricating lightweight structures with precision welding needs. - **Construction**: Utilized in the fabrication of metal frameworks, tunnels, and bridges. - **Art and Design**: Artists and fabricators use these welders for creating intricate metal sculptures and installations.
Conclusion
In conclusion, the All-in-One High Frequency Welder for Metal Processing stands at the forefront of technology in the manufacturing sector. Its innovative design and robust functionality converge to create a powerful tool that not only enhances productivity and quality but also offers significant cost savings. As industries continue to seek efficient solutions in metal fabrication, investing in high frequency welders will likely become an essential strategy for staying competitive in the market. With the advantages already highlighted, it is clear that the future of metal processing is bright with the integration of these versatile welding machines.