[High frequency welder for plastic]Exploring the Efficiency and Versatility of High Frequency Welders for Plastic Applications in Modern Industries
News 2024-12-31
In the dynamic landscape of modern manufacturing, the need for efficient and durable joining solutions is crucial, particularly for plastic materials. Among the various techniques employed, high frequency welding has emerged as a leading method for plastic welding. This article will delve into what high frequency welders are, how they operate, their advantages, applications, and their significance across diverse industries.
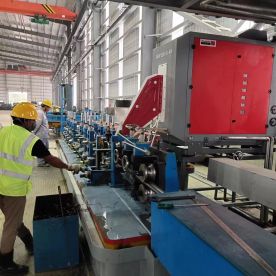
Exploring the Efficiency and Versatility of High Frequency Welders for Plastic Applications in Modern Industries
High frequency welding, also known as radio frequency (RF) welding or dielectric welding, involves using high-frequency electromagnetic waves to generate heat within the materials being joined, usually thermoplastic materials. The key mechanism at play is the dielectric heating effect: when an electric field is applied to a plastic, it causes the molecules to vibrate and generate heat. This local heating softens the material, allowing for the formation of a strong bond as the surfaces are pressed together.
High frequency welders for plastic are equipped with specialized electrodes that create a high-frequency electric field, typically ranging from 13.56 MHz to 40.68 MHz, effectively transferring energy into the plastic and promoting rapid fusion. This process is not only effective for bonding but can also be used for applications such as hemming, sealing, and even coating.
**Advantages of High Frequency Welding**
1. **Speed and Efficiency**: One of the most significant benefits of high frequency welding is its rapid processing time. The technology can weld parts in a matter of seconds, offering high throughput and productivity, which is vital in high-volume manufacturing environments.
2. **Strong, Durable Bonds**: The heat generated is localized, which means that the adjoining plastic parts achieve the necessary temperature for bonding without affecting the surrounding areas. This results in strong, durable joints that maintain the integrity of the material.
3. **Versatility**: High frequency welding can be utilized on various types of thermoplastics, including PVC, polyurethane, and polycarbonate, making it suitable for diverse applications across different industries, from automotive to textiles and medical devices.
4. **Cost-Effectiveness**: Even though the initial investment in high frequency welding machines may be higher than some other bonding techniques, the long-term savings in labor, material waste, and maintenance make it a cost-effective solution.
5. **Environmentally Friendly**: The process does not require adhesives or solvents, which not only cross-contaminates the product but can also pose environmental hazards. The absence of such materials in high frequency welding helps ensure a cleaner manufacturing process.
**Applications of High Frequency Welders for Plastic**
High frequency welding finds its applications in numerous industries due to its advantages. Here are some notable sectors employing this technology:
1. **Automotive Industry**: High frequency welding is widely used for joining various car components, such as dashboard covers, airbag housings, and upholstered parts. The robust nature of welds ensures safety and longevity in automotive applications.
2. **Medical Devices**: In the healthcare sector, high frequency welders produce medical components where sterility and strength are crucial. Items such as IV bags, surgical masks, and disposable medical supplies benefit from the precision and reliability of RF welding.
3. **Apparel and Fashion**: The textile industry utilizes high frequency welding for seamless garments and inflatable products. This method can create water-resistant seams in clothing, sports equipment, and outdoor gear, thus expanding design possibilities while maintaining quality.
4. **Packaging Industry**: Many companies in the packaging sector leverage high frequency welding for producing flexible packaging materials. The technology is essential for creating sealed pouches, wrappers, and other containers that require airtight seals.
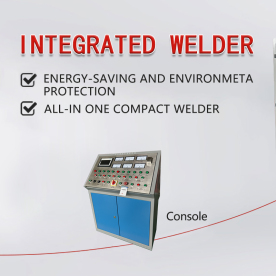
Exploring the Efficiency and Versatility of High Frequency Welders for Plastic Applications in Modern Industries
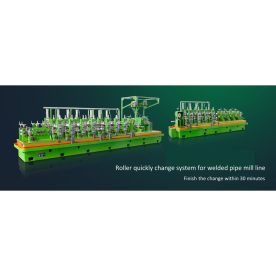
Exploring the Efficiency and Versatility of High Frequency Welders for Plastic Applications in Modern Industries
**Conclusion**
High frequency welders for plastic represent a significant advancement in joining technology that meets the needs of various industries with speed, efficiency, and eco-friendliness. As industries continue to innovate and find ways to enhance manufacturing processes, the role of high frequency welding will only grow more critical. Its benefits, alongside the demand for reliable plastic products, will ensure that this technology remains at the forefront of modern plastic fabrication solutions.