[Automatic high frequency welder]Exploring the Advantages and Innovations of Automatic High Frequency Welders in Modern Manufacturing Processes
News 2024-12-31
In the landscape of modern manufacturing, the quest for precision and efficiency has led to the evolution of welding technologies. Among these, the automatic high frequency welder stands out as a crucial innovation. This advanced tool provides manufacturers with enhanced speed, reliability, and quality in various welding applications, particularly in the construction of pipes, tubes, and various metal products. Let's delve into what makes automatic high frequency welders vital assets in contemporary manufacturing settings, their operational mechanisms, advantages, and industry applications.
Understanding Automatic High Frequency Welders
Automatic high frequency welding (AHFW) is a process that uses high-frequency electromagnetic energy to generate heat in the base metal. This method is widely utilized for welding thin-walled materials, where conventional welding techniques might not produce the required quality or integrity. The process involves feeding metal strips or wires through a welding machine, where they are subjected to alternating high-frequency currents. This causes the materials to heat up rapidly at the edges, allowing them to fuse together without the need for additional filler materials.
One of the primary characteristics of automatic high frequency welding is its efficiency. Once set up, the machine can operate in a fully automatic mode. Operators only need to monitor and adjust parameters as necessary, freeing them to focus on other aspects of production. Moreover, automatic high frequency welders are capable of achieving consistent weld quality, which is essential in industries where precision is non-negotiable, such as aerospace, automotive, and construction.
Advantages of Automatic High Frequency Welders
1. Enhanced Speed and Efficiency
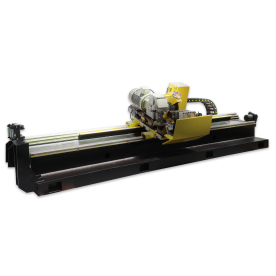
Exploring the Advantages and Innovations of Automatic High Frequency Welders in Modern Manufacturing Processes
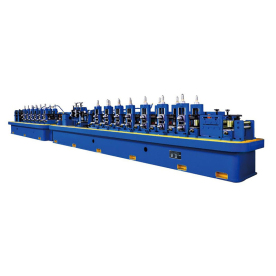
Exploring the Advantages and Innovations of Automatic High Frequency Welders in Modern Manufacturing Processes
The precise control over welding parameters afforded by automatic high frequency welders leads to superior weld quality. With the ability to maintain consistent temperature and control the weld profile, manufacturers can achieve stronger welds with minimal defects. This quality assurance is especially important in industries where safety and durability are paramount.
3. Reduced Heat-Affected Zone
Unlike traditional welding methods, which can create large heat-affected zones (HAZ), automatic high frequency welding concentrates heat at the weld interface. This technique minimizes distortion and maintains the integrity of the base material. By controlling the HAZ, manufactures can produce finished products that maintain the desired mechanical properties, as well as aesthetic quality.
4. Versatility in Application
Automatic high frequency welders are incredibly versatile, capable of working with various materials, including stainless steel, aluminum, and carbon steel. This adaptability makes them suitable for numerous applications across different industries. From fabricating steel pipes for oil and gas transportation to producing seamless tubes for medical devices, the utility of AHFW machines is virtually limitless.
5. Energy Efficiency
The high-frequency welding process is also noted for its energy efficiency. Since the heat generation is localized, less energy is wasted compared to traditional welding methods. As businesses strive for sustainability, adopting energy-efficient machinery like automatic high frequency welders can contribute to reduced operational costs and lower carbon footprints.

Exploring the Advantages and Innovations of Automatic High Frequency Welders in Modern Manufacturing Processes
Automatic high frequency welders are employed across a variety of industries. In the automotive sector, they are used for manufacturing components that require precise and durable welds. In the oil and gas industry, high-frequency welding is critical for producing strong, reliable pipelines that must withstand harsh environmental conditions. Additionally, they play a vital role in the manufacturing of HVAC systems and other industrial equipment.
Conclusion
The automatic high frequency welder represents a significant advancement in welding technology, offering a blend of speed, quality, and efficiency that traditional welding methods often lack. As industries continue to evolve and demand higher standards of precision and durability, the adoption of automatic high frequency welding processes is likely to expand. By embracing this cutting-edge technology, manufacturers can not only improve their production capabilities but also enhance the quality of their products, meeting the challenges of a competitive marketplace head-on.