[Cold cutting saw machine]Understanding the Efficiency and Precision of Cold Cutting Saw Machines in Metal Fabrication and Manufacturing Processes
News 2024-12-29
Cold cutting saw machines have revolutionized the landscape of metal fabrication and manufacturing by offering unparalleled precision, efficiency, and safety in cutting various materials. Unlike traditional cutting methods that generate excessive heat and waste, cold cutting saws operate by employing abrasive blades that achieve clean cuts without damaging the integrity of the material. This article will explore the workings, benefits, applications, and maintenance of cold cutting saw machines, shedding light on why they are increasingly becoming an essential tool in the metalworking industry.
**How Cold Cutting Saw Machines Work**
At the heart of a cold cutting saw machine is an abrasive blade that is designed to slice through metal with minimal heat generation. Unlike traditional band saws or circular saws that may use conventional blades, cold cutting saws utilize materials such as diamond or CBN (cubic boron nitride) for their blades, allowing for greater cutting durability and efficiency. As the blade approaches the material, it grinds rather than cuts, which produces very little heat. This method significantly reduces the risk of material warping or becoming structurally compromised.
Cold cutting saw machines often come equipped with advanced features, such as variable speed controls and programmable settings, enabling operators to adjust the cutting process according to the specific type and thickness of the material being worked on. Additionally, these machines may incorporate automatic feeding systems, reducing manual labor and increasing productivity.
**Benefits of Cold Cutting Saw Machines**
1. **Precision and Quality of Cuts**: One of the most significant advantages of cold cutting saw machines is their ability to produce clean, burr-free cuts. This high level of precision minimizes the need for secondary finishing processes, saving time and labor costs.
2. **Material Integrity**: As most cold cutting operations produce minimal heat, the risk of thermal distortion and hardening is significantly reduced. This allows for the preservation of the mechanical properties of the materials, ensuring that the finished product meets stringent quality standards.
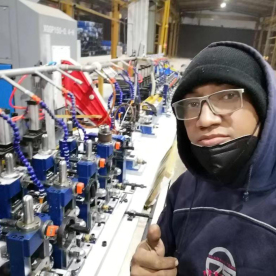
Understanding the Efficiency and Precision of Cold Cutting Saw Machines in Metal Fabrication and Manufacturing Processes
4. **Reduced Waste**: The grinding action of cold cutting minimizes waste, using material more efficiently than traditional cutting methods. This eco-friendly approach not only reduces the cost of raw materials but also makes a positive contribution to sustainability practices in manufacturing settings.
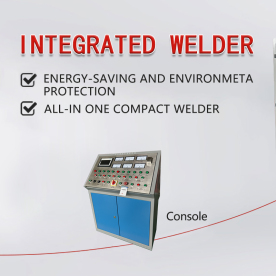
Understanding the Efficiency and Precision of Cold Cutting Saw Machines in Metal Fabrication and Manufacturing Processes
**Applications of Cold Cutting Saw Machines**
Cold cutting saw machines are versatile and can be found in various industries. Common applications include metal fabrication shops, automotive manufacturing, aerospace components, and even construction sites where precision cutting is paramount. These machines are ideal for producing parts, including pipes, tubes, structural steel components, and intricate shapes required in custom projects.
Moreover, as industries continue to innovate, the applications of cold cutting saws are expanding. They are now utilized in specialized fields such as robotics and renewable energy, where precision and reliability are critical.
**Maintenance of Cold Cutting Saw Machines**
To ensure longevity and optimal performance, regular maintenance of cold cutting saw machines is essential. Key maintenance practices include:
- **Regular Inspection**: Routinely check for blade wear, machine alignment, and overall functionality. - **Cleaning**: Keep the machine clean from debris and dust to avoid interference with moving parts. - **Lubrication**: Ensure that all moving parts are properly lubricated to minimize friction and wear.
Failure to perform regular maintenance can lead to decreased cutting performance and increased operational costs, negating the numerous advantages offered by cold cutting saw machines.
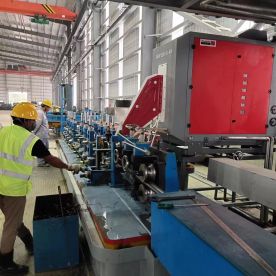