[All-in-one high frequency welder]Exploring the Advantages and Applications of All-in-One High Frequency Welder for Industrial Projects
News 2024-12-29
****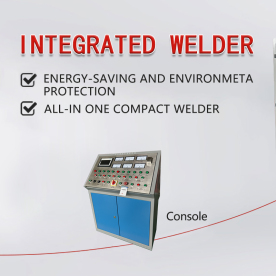
Exploring the Advantages and Applications of All-in-One High Frequency Welder for Industrial Projects
Understanding High Frequency Welding
High frequency welding, or HF welding, is a process that utilizes high-frequency electromagnetic fields to generate heat in conductive materials, effectively fusing them together. The All-in-One High Frequency Welder is designed to accommodate a variety of materials, such as thermoplastics, PVC, and polyolefins, making it a versatile option for manufacturers. Unlike traditional welding methods, which often rely on heat or pressure alone, HF welding offers faster and more consistent results, reducing production time and increasing efficiency.
Key Features
The All-in-One High Frequency Welder comes equipped with several essential features that enhance its performance:
1. **Versatility**: This welder can handle various types of materials and thicknesses, making it suitable for a wide range of applications. This adaptability allows manufacturers to use a single machine for multiple projects, reducing the need for specialized equipment.
2. **Automatic Operation**: Modern models come with programmable functions that can be customized according to specific project requirements. This automation minimizes human error and ensures uniformity in weld quality.
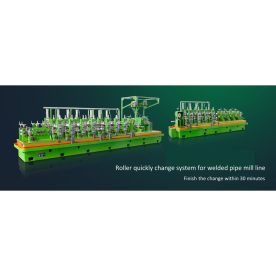
Exploring the Advantages and Applications of All-in-One High Frequency Welder for Industrial Projects
4. **Energy Efficiency**: These welders typically use less energy than traditional welding methods. This efficiency not only cuts down operational costs but also aligns with sustainable manufacturing practices, reducing the overall carbon footprint of production.
5. **Safety Features**: Advanced welders include safety mechanisms that prevent overheating, overloading, or electrical faults. Such features enhance operational safety and protect the investment in the equipment.
Advantages of Using All-in-One High Frequency Welder
1. **Speed of Operation**: One of the most significant benefits of HF welding is its rapidity. The welding process occurs within seconds, which drastically cuts down production times. This speed allows manufacturers to meet tight deadlines and increase output.
2. **Superior Weld Quality**: HF welding provides excellent fusion between materials, resulting in strong and durable seams. This quality is especially crucial in industries where product reliability is paramount, such as automotive and aerospace.

Exploring the Advantages and Applications of All-in-One High Frequency Welder for Industrial Projects
4. **Reduced Material Waste**: The precision of the welding process means that there is less scrap material generated, contributing to a more sustainable manufacturing process. This reduction not only lowers costs but also benefits the environment.
5. **Ease of Maintenance**: Compared to more complex welding systems, the All-in-One High Frequency Welder is usually easier to maintain. With fewer moving parts and straightforward design, operators can efficiently carry out routine checks and repairs, minimizing downtime.
Applications Across Industries
The versatility of the All-in-One High Frequency Welder has made it an indispensable tool across a multitude of sectors:
- **Automotive Industry**: Used for manufacturing automotive components, such as dashboards and interior trims, where strong, precise joints are essential for durability and aesthetics.
- **Textile and Fabrication**: Applied in producing outdoor gear, tarps, and banners, HF welding creates robust seals that withstand various weather conditions.
- **Packaging**: In the packaging industry, this technology is utilized for creating plastic bags, wrappers, and pouches that require airtight seals for product safety.
- **Medical Devices**: In the medical field, high-frequency welding is employed to manufacture sterile, airtight containers and components, ensuring strict hygiene standards.
- **Aerospace**: Selected for specialized components that require high reliability and performance under stress, the All-in-One High Frequency Welder contributes to the overall safety and efficiency of aerospace products.
In conclusion, the All-in-One High Frequency Welder is a groundbreaking advancement in welding technology, offering numerous advantages and applications across various industries. With its ability to deliver high-quality welds quickly and efficiently while minimizing material waste, it proves to be a valuable asset for any manufacturing operation. By investing in this innovative equipment, businesses can not only enhance their production capabilities but also contribute to more sustainable manufacturing practices.