[Pipe mill production line]Enhancing Efficiency and Quality in Manufacturing: An In-Depth Look at Pipe Mill Production Line Operations
News 2024-12-28
****In the ever-evolving landscape of manufacturing, the pipe mill production line stands out as a critical component in the fabrication of high-quality pipes for various applications. From oil and gas transmission to construction and infrastructure projects, the quality and efficiency of the pipe mill production process play a significant role in determining the overall success of these endeavors. This article delves into the intricacies of the pipe mill production line, exploring its components, processes, and the latest technological advancements that enhance productivity and quality.
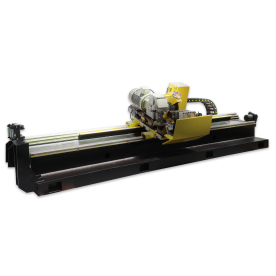
Enhancing Efficiency and Quality in Manufacturing: An In-Depth Look at Pipe Mill Production Line Operations
A pipe mill production line encompasses a series of interrelated processes designed to convert raw materials, typically steel or other metals, into high-quality pipes. The production line is carefully structured to ensure that each stage of the manufacturing process results in a product that meets rigorous quality standards.
Key components of a pipe mill production line include:
1. **Raw Material Preparation**: The production process begins with the preparation of raw materials. Steel coils or sheets are inspected for quality, and the appropriate materials are selected for the specific type of pipe being manufactured. This stage is critical, as the quality of raw materials directly impacts the final product's strength and durability.
2. **Forming Process**: The raw materials are then subjected to various forming processes such as hot or cold rolling, welding, or extrusion, depending on the desired pipe specifications. Forming methods are chosen based on factors such as pipe diameter, wall thickness, and planned application. Modern pipe mills may utilize advanced forming techniques to optimize the production process and enhance the mechanical properties of the pipes.
3. **Welding**: After forming, the next stage involves welding the edges of the formed material. This is crucial for creating seamless or welded pipes, ensuring that the pipe maintains structural integrity throughout its lifespan. Advanced welding technologies such as high-frequency induction (HFI) welding or electric resistance welding (ERW) are often employed, contributing to faster production speeds and improved quality.
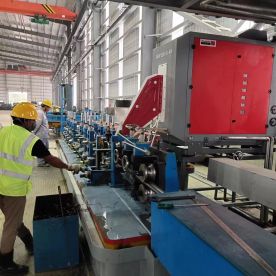
Enhancing Efficiency and Quality in Manufacturing: An In-Depth Look at Pipe Mill Production Line Operations
5. **Finishing Operations**: Once the pipes have been welded and treated, they undergo finishing operations, which include trimming, coating, and inspecting for defects. These finishing touches are essential for ensuring that the pipes are ready for their intended application and meet industry standards.
6. **Quality Control and Testing**: A robust quality control system is integral to any pipe mill production line. Each batch of pipes is subjected to rigorous testing, including pressure testing, dimensional inspections, and non-destructive testing methods like ultrasonic or radiographic tests. Quality control measures help identify any defects early in the production process, thereby reducing waste and ensuring that only products meeting specifications are shipped to clients.
**Technological Innovations Transforming Pipe Mill Production Lines**
In recent years, advancements in technology have significantly enhanced the efficiency and quality of pipe mill production lines. Automation and Industry 4.0 technologies, including the Internet of Things (IoT) and artificial intelligence (AI), are revolutionizing traditional manufacturing processes. These technologies enable real-time monitoring of the production line, predictive maintenance, and improved inventory management.
Furthermore, advanced data analytics tools allow manufacturers to analyze production data, identify bottlenecks, and optimize workflows, ultimately leading to increased productivity and reduced operational costs.
Sustainability is also becoming a focal point in the pipe manufacturing industry. Eco-friendly production techniques, such as recycling scrap materials and reducing energy consumption, are not only beneficial for the environment but also align with the growing demand for sustainable manufacturing practices.
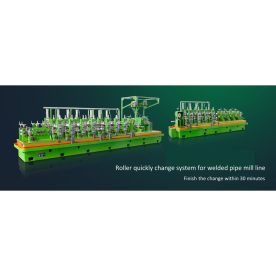
Enhancing Efficiency and Quality in Manufacturing: An In-Depth Look at Pipe Mill Production Line Operations
The pipe mill production line is a complex yet fascinating aspect of the manufacturing sector, playing a pivotal role in producing pipes for various applications. Understanding its components, processes, and the impact of technological innovations is essential for manufacturers aiming to stay competitive in today’s fast-paced marketplace. By focusing on quality, efficiency, and sustainability, the industry can continue to meet the evolving needs of customers while contributing to a more sustainable future.