[Solid state HF welder with remote control]Revolutionizing Fabrication Processes: The Benefits of Solid State HF Welder with Remote Control for Modern Industries
News 2024-12-28
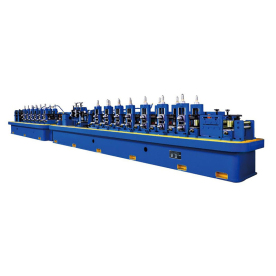
Revolutionizing Fabrication Processes: The Benefits of Solid State HF Welder with Remote Control for Modern Industries
In today's fast-paced manufacturing environment, efficiency and precision are paramount. As industries evolve, so does the technology that drives them. One noteworthy innovation in the field of welding is the Solid State High-Frequency (HF) welder equipped with remote control capabilities. This advanced technology has not only optimized the welding process but has also introduced unparalleled convenience, flexibility, and safety for operators in a variety of sectors.
What is Solid State HF Welding?
Solid State HF welding utilizes advanced semiconductor technology to generate high-frequency currents, which are essential for welding a variety of materials, particularly thermoplastics and metals. The process works by creating a high-frequency electromagnetic field that induces molecular agitation at the interface of the materials being joined. This agitation creates heat, causing the materials to fuse together without the need for additional filler materials or complex setups.
Traditional HF welding methods often rely on bulky transformers and sizeable mechanical components that can lead to inefficiencies and require extensive maintenance. The introduction of solid-state technology eliminates many of these concerns, resulting in a sleeker, more durable unit that offers enhanced performance and reduced downtime.
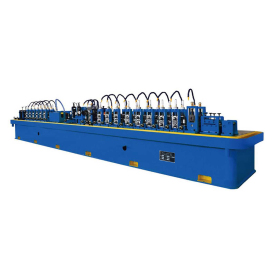
Revolutionizing Fabrication Processes: The Benefits of Solid State HF Welder with Remote Control for Modern Industries
The integration of remote control capabilities with solid state HF welders has transformed the way operators interact with these machines. Here are several key benefits of having remote control functionality:
1. **Increased Operator Safety**: Welding processes can be dangerous, with the potential for sparks, fumes, and other health hazards. By enabling remote operation, workers can maintain a safe distance from the welding area, reducing the risk of injury. Operators can monitor and control the process from a safe vantage point, ensuring that they avoid exposure to harmful elements.
2. **Improved Precision and Control**: Remote control technology allows operators to make real-time adjustments to the welding parameters. Whether it's adjusting the frequency, power levels, or time settings, the ability to control the welder from a distance means greater precision. This is crucial in industries where quality and consistency are key, such as aerospace and automotive manufacturing.
3. **Enhanced Flexibility**: Many solid state HF welders with remote controls offer the capability to operate multiple machines simultaneously. This multi-tasking ability is invaluable in high-volume production settings where time is a critical factor. Operators can oversee several machines from a single control point, optimizing workflow without the need for constant physical supervision.
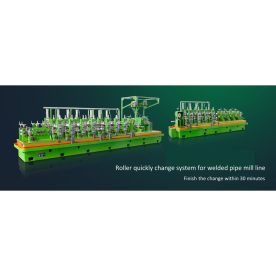
Revolutionizing Fabrication Processes: The Benefits of Solid State HF Welder with Remote Control for Modern Industries
5. **Data Collection and Analysis**: Many modern solid state HF welders come equipped with digital interfaces that facilitate data collection throughout the welding process. With remote monitoring capabilities, operators can track performance metrics, identify issues in real time, and make necessary adjustments instantly. This data-driven approach enhances quality control and supports predictive maintenance, leading to a more efficient operation.
Implementation Across Various Industries
Solid state HF welders with remote control are not limited to specific applications; they are utilized in a myriad of industries. For instance, in the automotive sector, they are crucial for assembling components such as dashboards, body panels, and wiring harnesses. In the packaging industry, they enable the efficient sealing of plastic materials, ensuring an airtight and hygienic product.
Moreover, these advanced welders have found their way into the medical device manufacturing sector, where precision and reliability are vital. Solid state HF welders help create components that meet stringent quality standards, ensuring that medical devices function correctly and safely.
Conclusion
The advent of solid state HF welders with remote control functionality signifies a major leap forward in welding technology. Their ability to enhance safety, improve precision, and reduce setup time makes them an invaluable asset in modern manufacturing environments. As industries continue to seek innovative solutions to increase productivity and quality, the adoption of these advanced welding machines is likely to grow, paving the way for a more efficient and safe future in fabrication. By embracing these technologies, businesses can maintain a competitive edge and meet the ever-increasing demands of the global market.