[ERW tube mill]Understanding the Importance of ERW Tube Mill in Modern Manufacturing: A Comprehensive Overview
News 2024-12-28
Introduction
In the evolving landscape of industrial manufacturing, the efficient production of steel tubes is pivotal, particularly in various sectors such as construction, automotive, and energy. One of the most significant advancements in this realm is the Electric Resistance Welded (ERW) tube mill. This article delves into the crucial role of ERW tube mills, exploring their technology, manufacturing processes, applications, advantages, and the future of ERW technology in the industry.
What is an ERW Tube Mill?
An ERW tube mill is a specialized machinery system designed for the production of welded steel tubes. The process involves forming flat strips of steel into tubular shapes, which are then welded together along the seam. The 'electric resistance welding' technology utilizes electric current to create heat, permitting the edges of the steel strips to fuse together without additional filler material. This method is renowned for producing strong, durable, and high-quality tubes that meet the diverse requirements of various industries.
The Manufacturing Process
The production cycle in an ERW tube mill can be broadly divided into several key stages:
1. **Material Preparation**: The process begins with the selection of high-quality steel strips. These strips are thoroughly inspected for any imperfections before proceeding to the mill.
2. **Forming**: The flat steel strip is then fed into a series of forming rolls. As the strip moves through these rolls, it gradually takes on a cylindrical shape.
3. **Welding**: Once the strip achieves a circular profile, it undergoes electric resistance welding. Electrodes apply current to the edges of the strip, heating them to a molten state and forming a strong bond.
4. **Cooling and Sizing**: Post-welding, the welded tube enters a cooling section where it is gradually cooled to room temperature. Following cooling, the tube is then sized to ensure consistency in diameter and wall thickness.
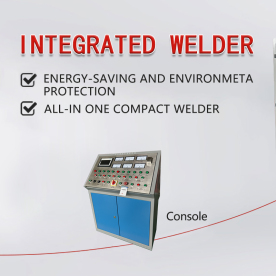
Understanding the Importance of ERW Tube Mill in Modern Manufacturing: A Comprehensive Overview
Applications of ERW Tubes
ERW tubes are used across a multitude of industries due to their versatility and design customization options. Some notable applications include:
- **Construction**: In infrastructure projects—such as buildings, bridges, and pipelines—ERW tubes are utilized for structural support and fluid transport. - **Automotive**: Manufacturers use ERW tubes for making car frames, exhaust systems, and other critical components, benefitting from the strength-to-weight ratio of these tubes.
- **Energy Sector**: ERW tubing plays a vital role in the oil and gas industry, particularly for transportation pipelines and casing tubes in drilling applications.
- **Furniture and Fabrication**: These tubes are also popular in furniture manufacturing due to their aesthetic appeal and sturdy construction.
Advantages of ERW Tube Mills
The adoption of ERW tube mills offers several advantages over traditional manufacturing processes:
1. **Cost-Effectiveness**: The efficiency of the ERW process reduces production costs, making it a preferred choice for manufacturers looking to optimize their operations.
2. **Uniform Quality**: The controlled manufacturing environment helps ensure consistent product quality, which is critical for applications with stringent specifications.
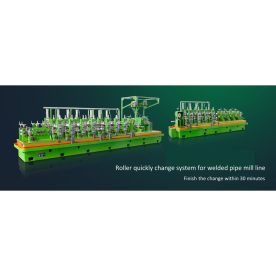
Understanding the Importance of ERW Tube Mill in Modern Manufacturing: A Comprehensive Overview
4. **Environmentally Friendly**: The process generates less waste compared to other manufacturing methods, contributing to sustainability efforts in the industry.

Understanding the Importance of ERW Tube Mill in Modern Manufacturing: A Comprehensive Overview
As technology progresses, the ERW tube mill is expected to undergo further advancements. Incorporation of automation and smart manufacturing principles, such as the Internet of Things (IoT), can enhance operational efficiency and predictive maintenance. Additionally, with the growing emphasis on sustainable practices, innovations in materials and energy consumption within ERW tube production will play a significant role.
Conclusion
In summary, the ERW tube mill stands as a cornerstone of modern tube manufacturing technology. Its efficiency, versatility, and ability to produce high-quality welded tubes make it an invaluable asset across various sectors. As industries evolve and demand for innovative solutions increases, the continuous development and integration of ERW technology will undoubtedly shape the future of manufacturing. As manufacturers and engineers recognize its potential, the significance of ERW tube mills in industrial applications is only expected to grow.