[Precision-control All-in-one Welding Equipment]Revolutionizing Metal Fabrication: The Rise of Precision-Control All-in-One Welding Equipment for Professionals and Hobbyists Alike
News 2024-12-26
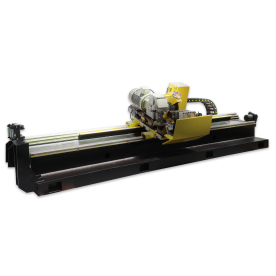
Revolutionizing Metal Fabrication: The Rise of Precision-Control All-in-One Welding Equipment for Professionals and Hobbyists Alike
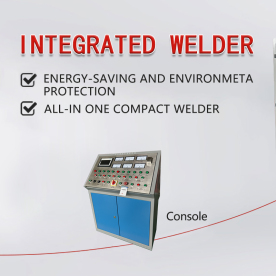
Revolutionizing Metal Fabrication: The Rise of Precision-Control All-in-One Welding Equipment for Professionals and Hobbyists Alike
One of the most significant advantages of these all-in-one systems is their precision control capabilities. These machines are equipped with advanced digital displays and user-friendly interfaces, enabling welders to easily adjust parameters like voltage, amperage, and wire feed speed. With precise control over these settings, welders can ensure consistent quality in their work, which is crucial when working on intricate projects or when high standards are required.
The ability to switch between different welding processes without changing equipment is not only convenient but also enhances productivity. For instance, a welder can quickly switch from MIG welding, ideal for thicker materials, to TIG welding, which provides the finesse required for thin metals or non-ferrous materials like aluminum. This adaptability significantly reduces downtime, allowing welders to tackle a greater variety of tasks within a shorter timeframe.
Moreover, contemporary precision-control all-in-one welding equipment is equipped with innovative features such as programmable settings and automated features. Some models allow users to create and store specific welding profiles tailored to different materials and product requirements, empowering welders to achieve repeatable results with minimal adjustments. This capability is particularly beneficial in industrial settings where consistency is essential, as it reduces the risk of defects and waste.
Safety is another critical concern in the welding industry, and modern all-in-one systems are designed with advanced safety features that protect both the operator and the equipment. Many units come with built-in thermal overload protection, ensuring that the machine does not overheat during prolonged use. Additionally, features like gas flow control and automatic shutdown mechanisms provide an extra layer of safety, making these machines suitable for both experienced professionals and those new to welding.
As the need for high-quality welding equipment continues to rise, manufacturers are investing heavily in research and development to create even more advanced precision-control all-in-one welding machines. This commitment to innovation is driving the industry forward, resulting in machines that are not only more efficient but also more environmentally friendly. Many of the latest models are designed to minimize energy consumption and reduce the amount of waste produced during the welding process.
The benefits of precision-control all-in-one welding equipment extend beyond performance enhancements; they also promote the accessibility of welding techniques to a broader audience. Hobbyists and DIY enthusiasts can leverage these advanced tools to take on complex projects with confidence, expanding the popularity of welding as a skill and art form.
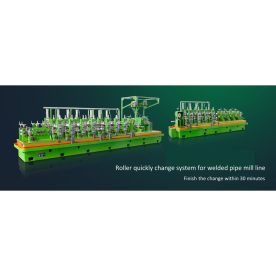