[Pipe mill production line]Exploring the Innovations and Processes of Pipe Mill Production Line: A Comprehensive Overview for Industry Professionals
News 2024-12-26
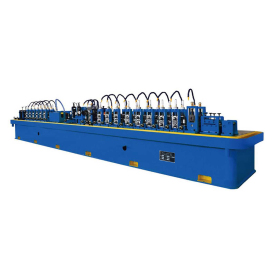
Exploring the Innovations and Processes of Pipe Mill Production Line: A Comprehensive Overview for Industry Professionals
Overview of Pipe Mill Production Line
A pipe mill production line typically consists of several critical processes that transform raw materials such as steel coils into finished pipe products. The main steps involve continuous forming, welding, sizing, and finishing, with additional processes for quality control and logistics management. The production line is designed to operate at high speeds while maintaining rigorous standards of quality and consistency.
Key Components of the Production Line
1. **Raw Material Handling**: The process begins with raw materials, such as hot-rolled or cold-rolled steel coils. Efficient handling systems are in place to store and feed these materials into the mill, ensuring minimal downtime and material waste.
2. **Forming Section**: In this section, coils are unwound and fed into a series of rollers. These rollers shape the steel into a pipe profile, which can be either round, square, or rectangular, depending on the product requirements. Advanced technology such as CNC-controlled rollers can enhance precision and speed during this crucial forming process.
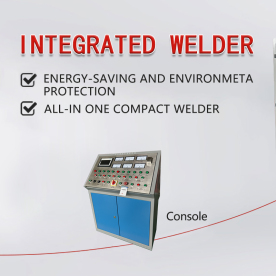
Exploring the Innovations and Processes of Pipe Mill Production Line: A Comprehensive Overview for Industry Professionals
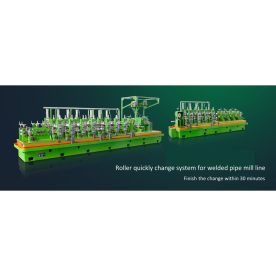
Exploring the Innovations and Processes of Pipe Mill Production Line: A Comprehensive Overview for Industry Professionals
5. **Finishing Process**: The finishing stage may include processes such as surface treatment, coating, and beveling. Surface treatment is vital for preventing corrosion, while coatings can enhance the durability and aesthetic of the pipes. Beveling is often necessary for preparing pipe ends for connections.
6. **Quality Control and Testing**: Quality control is paramount in the pipe production line. Various tests, including ultrasonic testing, hydrostatic testing, and visual inspections, are conducted to ensure that each pipe meets industry standards and specifications. Automated systems for quality control help in identifying defects early in the production process, reducing waste and maintaining quality.
Innovations in Pipe Mill Technology
As technology continues to advance, manufacturers are revolutionizing their pipe mill production lines. Automation and digitalization are becoming increasingly commonplace, with the introduction of smart systems that monitor production parameters in real time. These innovations not only enhance production efficiency but also improve traceability throughout the manufacturing process, allowing for better regulatory compliance and quality assurance.
Another noteworthy trend is the use of environmentally friendly practices. Many modern pipe mills are implementing sustainable practices, such as recycling waste materials and reducing water and energy consumption. Innovations in materials science are also leading to the development of high-strength, lightweight materials that can withstand greater stress and pressure, offering significant advantages in various applications.
Conclusion
In summary, the pipe mill production line is a complex yet fascinating system that is crucial in producing high-quality pipe products essential for numerous applications. Understanding the various stages of the production line, from raw material handling to final quality checks, allows industry professionals to appreciate the level of expertise and technology involved in the creation of pipes. With ongoing innovations, the future of pipe production looks promising, paving the way for enhanced efficiencies and sustainable practices that meet the needs of a growing global market. As industries evolve, so too will the techniques and technologies that define the pipe mill production line, ensuring it remains a vital component of modern manufacturing.