[Pipe mill production line with welding and cutting functions]Enhanced Efficiency and Precision: The Role of Pipe Mill Production Line with Welding and Cutting Functions in Modern Manufacturing
News 2024-12-26
In today’s fast-paced industrial landscape, the demand for high-quality pipes used in various applications is soaring. The essence of this demand is captured through the innovation found in pipe mill production lines, particularly those equipped with advanced welding and cutting functions. These lines not only enhance production efficiency but also ensure that the final products meet the ever-increasing quality standards imposed by various industries.
Pipe mill production lines are designed to handle the manufacturing of pipes from raw materials, typically steel, stainless steel, or other alloys. The process begins with the preparation of coils of strip steel, which are fed into the mill. The primary functions of modern pipe mills involve rolling the steel to the desired thickness and then using welding technology to join edges. This crucial step is integral as it determines the structural integrity and functionality of the pipes.
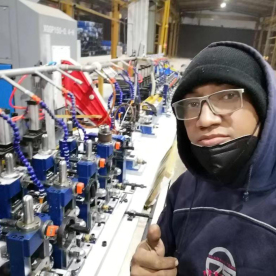
Enhanced Efficiency and Precision: The Role of Pipe Mill Production Line with Welding and Cutting Functions in Modern Manufacturing
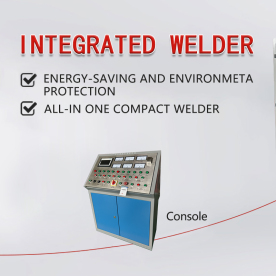
Enhanced Efficiency and Precision: The Role of Pipe Mill Production Line with Welding and Cutting Functions in Modern Manufacturing
The incorporation of cutting functions in the production line complements the welding capabilities, forming a comprehensive approach to pipe manufacturing. Once the pipes are welded, they often require precise cutting to specific lengths as dictated by project specifications or customer requirements. The cutting operation can include both mechanical and laser cutting techniques, each providing distinct advantages. Laser cutting, for instance, offers a high degree of precision, allowing manufacturers to cut pipes to exact lengths without additional finishing processes. This precision not only minimizes waste but also accelerates the production timeline.
Furthermore, the automation of both welding and cutting introduces enhanced operational efficiency. By employing computer numerical control (CNC) systems, manufacturers can optimize the workflow, reducing human error and improving consistency. Automation also enables real-time monitoring of the production process, ensuring that any potential issues can be addressed promptly before they escalate into costly downtime. This is particularly important as manufacturers strive to improve their return on investment while decreasing operational costs.
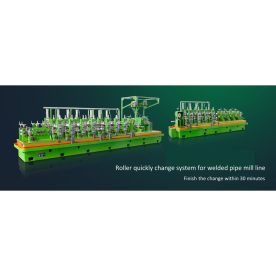
Enhanced Efficiency and Precision: The Role of Pipe Mill Production Line with Welding and Cutting Functions in Modern Manufacturing
In conclusion, the evolution of pipe mill production lines with advanced welding and cutting functions is a testament to the manufacturing industry's commitment to quality and efficiency. As demand for high-performance pipes grows across sectors, including construction, oil and gas, and infrastructure, leveraging these advanced technologies will be pivotal for manufacturers seeking a competitive edge. By investing in modern production lines that prioritize precision in welding and cutting, manufacturers not only improve their operational efficiency but also position themselves favorably in a marketplace that values quality and reliability. The future of pipe manufacturing lies in these interconnected systems that streamline processes, reduce waste, and deliver exceptional products to meet the dynamic needs of today’s industries.