[Customized Mould for Tube Mill Components]Enhancing Efficiency and Precision in Manufacturing: The Importance of Customized Mould for Tube Mill Components
News 2024-12-23
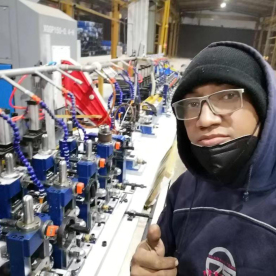
Enhancing Efficiency and Precision in Manufacturing: The Importance of Customized Mould for Tube Mill Components
Understanding Tube Mill Components
Before delving into the significance of customized moulds, it's essential to understand what tube mill components are and their roles in the manufacturing process. Tube mills are specialized machines used to produce welded or seamless tubes from flat metal sheets. This process involves several stages, including forming, welding, and sizing. Each of these stages requires specific components, such as rolls, guides, and dies, which dictate the end product's quality, size, and shape.
The Challenge of Standardization
Traditionally, many manufacturers relied on standardized moulds to produce tube mill components. While this approach can work for some, it often leads to inefficiencies and compromises in quality. Standard moulds may not provide the exact dimensions or tolerances required by specific applications, leading to increased waste, rework, and frustration. Furthermore, as industries evolve and demand more complex and specialized tubes, the need for customized solutions has become even more apparent.
Benefits of Customized Mould for Tube Mill Components
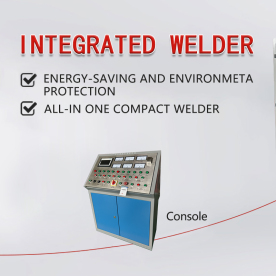
Enhancing Efficiency and Precision in Manufacturing: The Importance of Customized Mould for Tube Mill Components
2. **Enhanced Performance**: Customized moulds can be tailored to improve the performance characteristics of the components. For instance, specific designs can enhance the flow of materials during the forming process, resulting in superior surface finishes, increased strength, and improved durability.
3. **Cost Efficiency**: While the initial investment in customized moulds may be higher than standard options, the long-term cost savings can be significant. Custom moulds can reduce material waste, lower labor costs through streamlined processes, and minimize downtime due to fewer defects or failures.
4. **Flexibility and Adaptability**: In a rapidly changing marketplace, the ability to adapt and produce a wide variety of tube types and sizes is crucial. Customized moulds allow manufacturers to pivot quickly to meet new demands, whether for specialized fabrication or unique dimensions that differ from previous products.
5. **Improved Product Quality**: The superior fit and finish achieved through customized moulds lead to a higher quality end-product. This improvement in quality can enhance customer satisfaction and lead to increased loyalty and repeat business.
Implementing Customized Mould Solutions
To implement customized mould for tube mill components effectively, manufacturers should consider several steps:
- **Collaboration with Experts**: Engage with engineers and designers who specialize in mould creation. Their expertise can ensure that the moulds meet both technical and practical requirements.
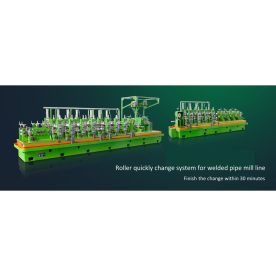
Enhancing Efficiency and Precision in Manufacturing: The Importance of Customized Mould for Tube Mill Components
- **Continuous Testing and Feedback**: Implement a system for testing the effectiveness of customized moulds and gather feedback from the manufacturing floor. This feedback loop can guide future improvements and innovations.
- **Quality Control**: Establish strict quality control measures to monitor the performance of customized moulds over time. Ensuring consistency in production is vital for maintaining quality standards.
Conclusion
In summary, the significance of customized mould for tube mill components cannot be overstated. As industries demand higher quality, greater precision, and increased efficiency, the reliance on bespoke solutions will only grow. By embracing customized mould designs, manufacturers can position themselves at the forefront of innovation, meeting the evolving needs of their clients while enhancing profitability and operational efficiency. In a sector where every fraction of a millimeter counts, the value of customized solutions is clear—precision, performance, and productivity all begin with the right mould.