[Automated All-in-one Welding Tool]Revolutionizing Welding: How the Automated All-in-One Welding Tool is Transforming Industrial Practices and Enhancing Efficiency
News 2024-12-23
In an era where technology is advancing at an extraordinary pace, industries are continuously evolving to enhance productivity, efficiency, and safety. One of the most significant innovations making waves across manufacturing and construction environments is the Automated All-in-One Welding Tool. This groundbreaking device is transforming traditional welding practices, integrating multiple functionalities that simplify the welding process while delivering exceptional quality and reliability.
The Automated All-in-One Welding Tool embodies the fusion of advanced robotics, artificial intelligence, and user-friendly interfaces. Designed to accommodate various welding techniques, such as MIG, TIG, and stick welding, this tool can meet the demands of diverse projects, from intricate assemblies to heavy-duty structural components. Its ability to automatically adjust parameters for different materials and thicknesses enables manufacturers to reduce setup times and minimize human error, thus optimizing operations and enhancing the final product's quality.
One of the primary advantages of the Automated All-in-One Welding Tool is its versatility. Traditional welding systems often require multiple machines for different processes. In contrast, this all-in-one solution combines several functionalities into a single unit. This integration streamlines workflow, allowing operators to switch seamlessly between welding tasks without the need for extensive reconfiguration or the cumbersome movement of equipment. As a result, productivity increases, and projects can be completed on schedule with fewer delays associated with equipment changes and troubleshooting.
Moreover, the Automated All-in-One Welding Tool is equipped with state-of-the-art sensing and feedback mechanisms. These features enable the machine to monitor real-time data during welding processes, allowing for immediate adjustments to variables such as amperage, voltage, and travel speed. This adaptive control mechanism ensures consistent welding quality, reduces the likelihood of defects, and minimizes the need for post-weld inspections or rework. As manufacturers strive for higher quality standards and compliance with rigorous industry regulations, this tool becomes an indispensable asset in maintaining competitive advantage.
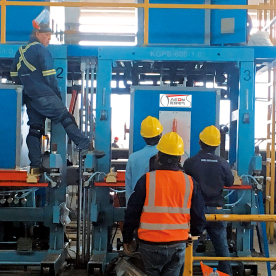
Revolutionizing Welding: How the Automated All-in-One Welding Tool is Transforming Industrial Practices and Enhancing Efficiency
Furthermore, the adoption of such cutting-edge technology aligns with broader trends toward sustainability and environmental responsibility. The Automated All-in-One Welding Tool is designed to improve material efficiency, significantly minimizing waste during the welding process. By optimizing welding conditions, the tool can also reduce energy consumption and lower the carbon footprint associated with metal fabrication. As sustainability becomes a critical focus for industries around the globe, businesses utilizing this advanced welding solution position themselves as leaders in responsible manufacturing practices.
Training and upskilling of workers are additional considerations that industries face when integrating new technology into existing workflows. The user interface of the Automated All-in-One Welding Tool has been developed with simplicity in mind, thus reducing the learning curve for new users. Online tutorials, training modules, and user-friendly manuals ensure that employees can quickly become proficient with the technology, maximizing its benefits and minimizing downtime associated with onboarding.
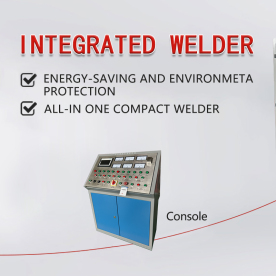
Revolutionizing Welding: How the Automated All-in-One Welding Tool is Transforming Industrial Practices and Enhancing Efficiency
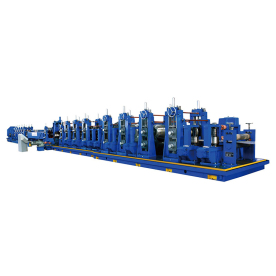