[Customized ERW tube mill solutions]Unlocking Industrial Potential with Customized ERW Tube Mill Solutions: Tailored Technologies for Enhanced Manufacturing Efficiency
News 2024-12-22
In the ever-evolving landscape of manufacturing and industrial production, the demand for precision-engineered components continues to escalate. Industries ranging from construction to automotive heavily rely on high-quality tubular products, leading to an intensified focus on the manufacturing processes that produce them. Among these processes, Electric Resistance Welding (ERW) tube mill technology stands out, delivering efficiency and versatility. However, to truly meet the unique needs of diverse applications, many manufacturers are turning towards customized ERW tube mill solutions.
At the heart of customized ERW tube mills is the idea that one size does not fit all. Every industry has its special requirements based on the end-use of the tubular products. In traditional manufacturing, tube mills could be somewhat limited in their designs and functionalities, often leading to inefficiencies and wasted production time. Customized ERW tube mill solutions bend these limitations, offering tailored machinery that aligns closely with specific operational needs.
**Understanding ERW Technology**
Before delving further into customized solutions, understanding how ERW technology operates is essential. Electric Resistance Welding refers to the process of welding two pieces of metal together using electric current. When metal sheets are fed into the ERW mill, they undergo a series of shaping and welding processes, where the edges are heated and bonded together, forming a tubular shape. This method is known for producing strong, high-quality welds, leading to robust and reliable products.
**Benefits of Customized ERW Tube Mill Solutions**
1. **Tailored Designs**: Customization allows for personalized designs that cater to the specific requirements of a manufacturer. Whether it’s producing tubes of varying diameters, wall thicknesses, or shapes, customized ERW tube mills ensure that the resulting products meet stringent industry standards.
2. **Increased Productivity**: Customized solutions often integrate advanced technologies that enhance overall productivity. For instance, specific changes in machinery setup can reduce downtime, streamline production, and decrease scrap rates. This efficiency translates to better output and profitability.
3. **Versatility**: Industries are not static. With market demands changing frequently, a customized ERW tube mill can adapt to the production of different tube specifications with relative ease. This flexibility not only minimizes the need for substantial capital investment in new machinery but also allows manufacturers to pivot quickly in response to market trends.
4. **Improved Quality Control**: When manufacturing processes are tailored, it becomes easier for manufacturers to monitor and maintain quality control throughout production. Customized tube mills often include advanced monitoring systems that allow for real-time feedback, ensuring that any deviations from quality standards can be swiftly addressed.
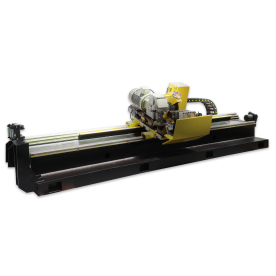
Unlocking Industrial Potential with Customized ERW Tube Mill Solutions: Tailored Technologies for Enhanced Manufacturing Efficiency
**Implementation of Customized Solutions**
The journey towards integrating customized ERW tube mill solutions begins with assessing the specific needs of the production line. This includes analyzing the types of tubes required, the materials being used, and the anticipated production volumes. Manufacturers can work with specialized providers who offer consultation services to outline their distinct requirements, helping them select the most effective features and technologies for their mills.
Furthermore, the implementation phase should not be overlooked. Successful integration of customized solutions necessitates thorough staff training and maintenance planning. Continuous support and upgrades ensure that the machinery operates at optimal levels throughout its lifecycle.
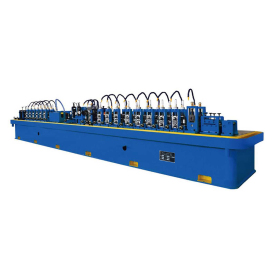
Unlocking Industrial Potential with Customized ERW Tube Mill Solutions: Tailored Technologies for Enhanced Manufacturing Efficiency
As technology evolves, the future of customized ERW tube mill solutions looks promising. With advancements like Industry 4.0, artificial intelligence, and automation becoming more prevalent, manufacturers are poised to further enhance their production processes. Predictive maintenance, advanced demand forecasting, and streamlined operations could soon become the standard across industries utilizing ERW tube mill technology.
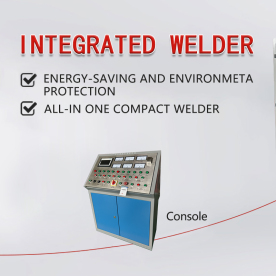