[Customized pipe mill production line solutions]Tailored Solutions for Customized Pipe Mill Production Line: Enhancing Efficiency and Quality in Pipe Manufacturing
News 2024-12-20
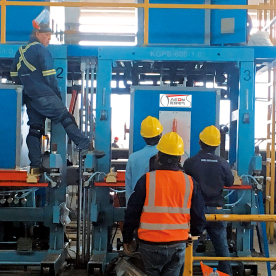
Tailored Solutions for Customized Pipe Mill Production Line: Enhancing Efficiency and Quality in Pipe Manufacturing
In today’s fast-paced manufacturing environment, the need for customized pipe mill production line solutions has never been more critical. The demand for tailored pipe manufacturing processes stems not only from diversified market needs but also from the evolving technology and materials in the industry. Businesses that utilize customized production lines can achieve enhanced efficiency, quality, and productivity, helping them to stay ahead of the competition.
The essence of a customized pipe mill production line solution lies in its ability to adapt to the specific requirements of different businesses. This adaptability is essential in addressing various factors such as material type, pipe diameter, wall thickness, shape, and even manufacturing volume. A one-size-fits-all approach is no longer viable; instead, manufacturers must embrace flexibility and specialization in their production processes.
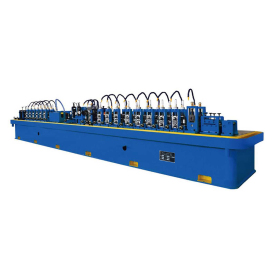
Tailored Solutions for Customized Pipe Mill Production Line: Enhancing Efficiency and Quality in Pipe Manufacturing
Customized pipe mill production lines are designed to meet the unique needs of pipe manufacturers, accommodating specific product requirements and operational goals. These solutions can involve a complete overhaul of existing systems or the integration of new machines and technologies into current setups. The ultimate goal is to improve the overall efficiency of the production process while maintaining high-quality standards.
The customization process begins with a comprehensive assessment of the manufacturer’s needs. This involves analyzing production volumes, existing equipment capabilities, desired outputs, and potential areas for improvement. By understanding these parameters, manufacturers can work with solution providers to tailor production lines that will optimize their workflows.
Key Components of Customized Pipe Mill Production Lines
1. **Raw Material Handling**: The handling of raw materials is critical in pipe production. Customized solutions ensure that the materials are fed into the production line efficiently and without damaging them. This process may include automated systems for loading coils or sheets, reducing manual labor and minimizing handling errors.
2. **Forming and Welding Processes**: The core of any pipe mill lies in its ability to form and weld materials efficiently. Customized production lines utilize state-of-the-art technology such as high-frequency induction welding, longitudinal and spiral forming methods, and advanced tooling systems. These technologies ensure precise pipe formation and superior weld quality, which translates directly into product durability and performance.
3. **Sizing and Calibration Equipment**: Accuracy is paramount in pipe manufacturing. Customized solutions include advanced sizing mills and calibration stations that ensure pipes meet the exact specifications required by clients. This ensures that every pipe produced is consistent in dimensions and tolerances, which is especially important in industries such as construction and oil and gas.
4. **Quality Control Systems**: An integral part of a customized pipe mill production line is the inclusion of robust quality control mechanisms. Automated inspection systems, such as ultrasonic or x-ray testing, can be integrated into the line to provide real-time feedback regarding product quality. This allows manufacturers to address issues instantly and maintain a high level of quality assurance.
5. **Automation and Data Management**: In an age driven by technology, automation plays a vital role in enhancing the efficiency of customized pipe mill production lines. Integrating advanced manufacturing execution systems (MES) can help manage production data, optimize workflows, and improve output tracking. Data analysis tools can provide insights into production efficiency, allowing for continuous improvement over time.
Benefits of Customized Pipe Mill Production Lines
The benefits of implementing customized pipe mill production lines are multifaceted. Firstly, they lead to improved operational efficiency. By tailoring the production line to the specific needs of the manufacturer, cycle times can be reduced, and production bottlenecks can be minimized. This boosts overall productivity.
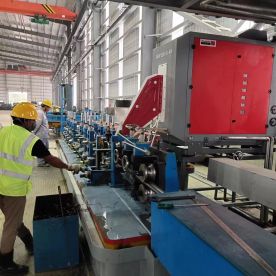
Tailored Solutions for Customized Pipe Mill Production Line: Enhancing Efficiency and Quality in Pipe Manufacturing
Finally, businesses can enjoy increased flexibility with customized pipe mill production lines. As market demands evolve, manufacturers can adjust their production processes to accommodate new product lines or specifications without undergoing a complete system overhaul. This adaptability is crucial for maintaining competitiveness in a rapidly changing market.
Conclusion
In conclusion, customized pipe mill production line solutions are essential for modern pipe manufacturers seeking to optimize their production capabilities. By investing in tailored systems that enhance efficiency, ensure product quality, and provide flexibility, manufacturers can position themselves for success in an increasingly competitive landscape. As the industry evolves, the adoption of such specialized solutions will undoubtedly be a key factor in driving future growth and innovation.