[Customized Mould for Tube Mill Components]The Importance of Customized Mould for Tube Mill Components: Enhancing Efficiency and Precision in Manufacturing Processes
News 2024-12-20
In the manufacturing industry, precision and efficiency are paramount, particularly in processes such as tube milling. Tube mills serve a critical function in producing tubular components that are widely used across various sectors, including automotive, aerospace, and construction. One of the key factors that can impact the quality of the final product and the overall production efficiency is the use of customized mould for tube mill components. This article delves into the significance of customized moulds in the production process, outlining their benefits, applications, and considerations for manufacturers seeking to optimize their operations.
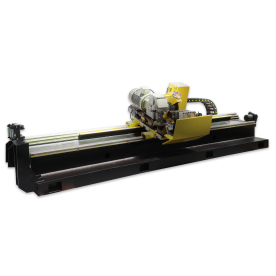
The Importance of Customized Mould for Tube Mill Components: Enhancing Efficiency and Precision in Manufacturing Processes
One of the primary advantages of using customized moulds is the improvement in product quality. When moulds are designed specifically for individual tube mill components, they can accommodate unique geometries and features that standardized moulds might not effectively replicate. This leads to a superior fit and finish, reducing the need for additional machining and finishing processes that can prolong production time and increase costs. In industries where precision is crucial, such as aerospace and automotive, the quality of the components can have a direct impact on safety and performance.
Moreover, customized moulds can significantly enhance the efficiency of the manufacturing process. By designing moulds that align perfectly with the production requirements, manufacturers can reduce cycle times and increase output. This efficiency is particularly vital in sectors where time-to-market is critical; being able to produce high-quality components quickly can provide a competitive edge. Furthermore, the use of tailored moulds can minimize material waste, as they can be configured to utilize raw materials more effectively, resulting in cost savings and a lower environmental impact.
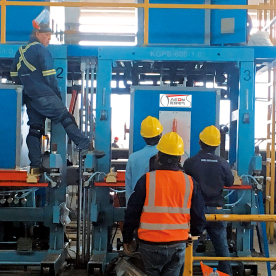
The Importance of Customized Mould for Tube Mill Components: Enhancing Efficiency and Precision in Manufacturing Processes
The development of customized moulds requires a collaborative approach between design engineers, production teams, and the end-users of the components. Understanding the specific requirements of the tube mill components being produced and the intended application is essential for creating effective mould designs. Advanced technologies such as Computer-Aided Design (CAD) and 3D printing play a significant role in this development process, allowing for rapid prototyping and testing of mould designs before full-scale production.
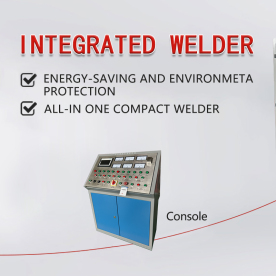
The Importance of Customized Mould for Tube Mill Components: Enhancing Efficiency and Precision in Manufacturing Processes
Additionally, the maintenance and upkeep of customized moulds should be part of the planning process. Just like any piece of equipment, customised moulds require regular maintenance to ensure they continue to perform effectively over time. Regular inspection, cleaning, and timely repairs will prolong the life of the moulds and maintain the quality standards of the tube components produced.
In conclusion, the significance of customized mould for tube mill components cannot be overstated. By investing in tailored mould designs, manufacturers can achieve higher quality products, improved production efficiency, and enhanced flexibility to adapt to market demands. As industries continue to evolve, staying ahead of the competition will increasingly depend on the ability to deliver superior components, and customized moulds play a pivotal role in this equation. By embracing the benefits of customized solutions, manufacturers can position themselves for success in a dynamic and competitive landscape.