[Vertical accumulator]Understanding the Role and Functionality of Vertical Accumulators in Modern Industrial Operations
News 2024-12-20
In the world of industrial operations, efficiency and optimized performance are paramount. Among the many components that contribute to this, vertical accumulators stand out as essential devices that enhance the functionality of hydraulic systems. This article delves into the intricacies of vertical accumulators, examining their design, functionality, applications, and the advantages they bring to various sectors.
What is a Vertical Accumulator?
A vertical accumulator is a type of hydraulic device designed to store and manage hydraulic fluid. Typically, these devices are engineered as cylindrical tanks that can stand upright, distinguishing them from their horizontal counterparts. This vertical orientation often allows for a more compact design, making them ideal for environments where space is at a premium. The main purpose of these accumulators is to store potential energy in the form of hydraulic fluid under pressure.
How Do Vertical Accumulators Work?
Vertical accumulators use a piston or bladder inside a rigid casing filled with hydraulic fluid and gas. When the hydraulic system experiences a spike in demand—or if pressure drops—the accumulator releases stored energy by allowing the hydraulic fluid to flow into the system. Conversely, when the system generates excess pressure, the fluid is sent back into the accumulator for storage.
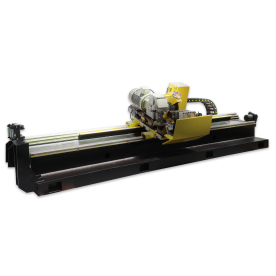
Understanding the Role and Functionality of Vertical Accumulators in Modern Industrial Operations
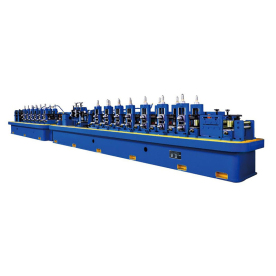
Understanding the Role and Functionality of Vertical Accumulators in Modern Industrial Operations
1. **Cylindrical Shell**: This is the outer casing that provides structural integrity and houses the hydraulic fluid. 2. **Piston or Bladder**: The internal component that separates the hydraulic fluid from the gas (typically nitrogen). This helps maintain pressure and allows the accumulator to store energy efficiently.
3. **Gas Chamber**: A space above the hydraulic fluid that contains pressurized gas, which aids in creating the necessary force for fluid movement.
4. **Fluid Ports**: Entry and exit points that connect the accumulator to the hydraulic system, allowing for fluid transfer when needed.
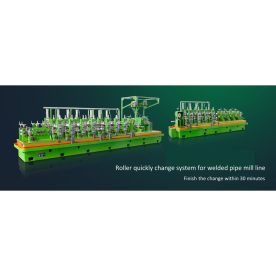
Understanding the Role and Functionality of Vertical Accumulators in Modern Industrial Operations
Vertical accumulators are employed across various industries due to their versatility and efficiency. Some of the most common applications include:
1. **Hydraulic Presses**: Used in manufacturing settings where consistent pressure is vital, vertical accumulators help efficiently manage the hydraulic fluid.
2. **Machine Tools**: In various machining processes, these devices buffer fluctuations in pressure and ensure a steady flow of hydraulic fluid.
3. **Automotive Systems**: Vertical accumulators play a crucial role in braking systems and other hydraulic functions in vehicles, providing quick response times and safety.
4. **Energy Recovery Systems**: In renewable energy settings, such as wind or solar energy applications, vertical accumulators can store hydraulic energy for later use, contributing to overall efficiency.
5. **Water Treatment Facilities**: Used to manage pressure fluctuations and ensure a constant flow of treatment chemicals, enhancing performance in processing systems.
Advantages of Vertical Accumulators
- **Space Efficiency**: Their vertical design makes them an excellent option for environments with limited horizontal space. - **Improved Response Times**: By providing immediate access to stored hydraulic energy, vertical accumulators can facilitate quick responses to changes in demand.
- **Reduced Pump Operation**: These accumulators can lead to decreased operation times for hydraulic pumps, resulting in lower energy consumption and extended pump life.
- **Enhanced System Stability**: They help maintain a consistent pressure level in hydraulic systems, which is crucial for overall stability and reliability.
- **Lower Maintenance Costs**: With fewer moving parts compared to other hydraulic systems, vertical accumulators generally require less maintenance, translating into cost savings over time.
Conclusion
Vertical accumulators play a critical role in enhancing the performance and efficiency of hydraulic systems in modern industrial operations. Their unique design, ability to manage pressure changes, and versatility across various applications make them indispensable components in many settings. As industries continue to seek efficiencies in operations, the relevance of vertical accumulators will only increase, ensuring that they remain a focal point in hydraulic engineering and design. Understanding their functionality and applications can provide valuable insights into improving industrial processes and systems, ultimately contributing to operational excellence and sustainability.