[High-Wear-Resistant Spare Parts for Tube Mills]Maximizing Efficiency and Longevity: The Importance of High-Wear-Resistant Spare Parts for Tube Mills in Modern Manufacturing
News 2024-12-19
In the highly competitive landscape of modern manufacturing, tube mills play a crucial role in producing high-quality steel pipes and tubes used across various industries. As demands for production efficiency and durability rise, the significance of using high-wear-resistant spare parts for tube mills cannot be overstated. These components directly influence operational efficiency, maintenance costs, and the overall lifespan of the equipment. This article explores the importance of high-wear-resistant spare parts for tube mills, their advantages, and best practices for their selection and maintenance.
Understanding Tube Mills and Their Applications
Tube mills are specialized machines designed to manufacture tube-shaped products from metal sheets or strips. They are primarily utilized in sectors such as construction, automotive, furniture, and energy. The manufacturing process involves several stages, including uncoiling, forming, welding, and sizing. Each stage of the process requires various components, such as rolls, bearings, and cutting tools, all of which face significant wear and tear due to the demanding operational environment.
Given the constant strain placed on these parts, using regular components can lead to frequent breakdowns, affecting overall productivity. Therefore, investing in high-wear-resistant spare parts becomes essential for ensuring consistent output and minimizing downtime.
The Impact of Wear and Tear on Tube Mills
As tube mills continuously operate under high pressure and speed, wear and tear become inevitable. Common issues associated with wear include the following:
1. **Loss of Precision**: Worn-out components can lead to inadequate shaping, sizing, and welding of tubes, resulting in out-of-spec products. 2. **Increased Downtime**: Frequent breakdowns due to component failure can halt production, leading to increased operational costs and potential loss of clientele.
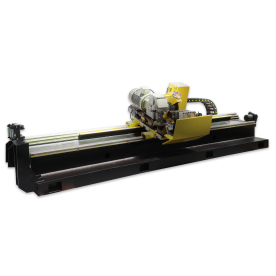
Maximizing Efficiency and Longevity: The Importance of High-Wear-Resistant Spare Parts for Tube Mills in Modern Manufacturing
4. **Safety Risks**: Worn components can become hazardous during operation, posing risks to workers and equipment.
Advantages of High-Wear-Resistant Spare Parts
Investing in high-wear-resistant spare parts yields numerous benefits for manufacturers operating tube mills:
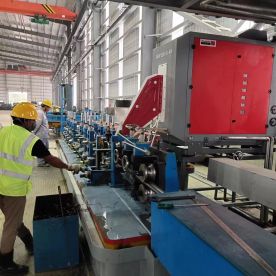
Maximizing Efficiency and Longevity: The Importance of High-Wear-Resistant Spare Parts for Tube Mills in Modern Manufacturing
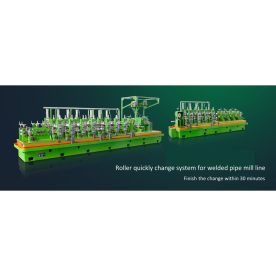
Maximizing Efficiency and Longevity: The Importance of High-Wear-Resistant Spare Parts for Tube Mills in Modern Manufacturing
2. **Improved Productivity**: By reducing the frequency of maintenance and replacement, manufacturers can maintain a higher level of productivity, minimizing costly downtime.
3. **Better Product Quality**: High-quality components improve the precision of the manufacturing process, leading to higher-quality finished products that meet stringent industry standards.
4. **Cost-Effectiveness**: Although high-wear-resistant spare parts may come with a higher initial investment, their overall long-term savings in terms of reduced maintenance, downtime, and enhanced productivity make them a cost-effective choice.
Selecting the Right High-Wear-Resistant Spare Parts
Choosing the right high-wear-resistant spare parts for tube mills requires careful consideration of various factors:
1. **Material Composition**: Understanding the material properties of spare parts is essential. Components made from materials engineered to withstand abrasion, impact, and corrosion can significantly enhance performance.
2. **Manufacturer Reputation**: Opt for reputable manufacturers known for producing high-quality, reliable spare parts. Doing so minimizes the risk of faulty components that could compromise production.
3. **Compatibility**: Ensure the selected spare parts are compatible with existing tube mill machinery. Incompatibility can lead to operational issues and increased wear.
4. **Testing and Certification**: Look for spare parts that meet industry standards and have undergone rigorous testing for durability and performance.
Maintenance Practices
Implementing effective maintenance practices is essential to maximize the benefits of high-wear-resistant spare parts:
1. **Regular Inspections**: Frequent assessments can help identify wear and tear before they lead to significant issues, allowing for timely replacements.
2. **Lubrication and Cleaning**: Maintaining proper lubrication and cleanliness can prevent excessive wear on components and keep the machinery running smoothly.
3. **Training Staff**: Equipping operators and maintenance personnel with the knowledge to handle and care for high-wear-resistant parts can further enhance their effectiveness.
Conclusion
High-wear-resistant spare parts for tube mills represent a pivotal investment in ensuring operational efficiency, product quality, and overall cost-effectiveness in manufacturing processes. By selecting quality components and implementing rigorous maintenance practices, manufacturers can significantly extend the lifespan of their tube mills while reducing downtime and maintaining a competitive edge in the industry. In an era where productivity is paramount, prioritizing wear-resistant components may very well be the key to sustained success.