[Precision Tube making equipment]Exploring the Latest Innovations in Precision Tube Making Equipment: Advancements, Applications, and Future Trends
News 2024-12-19
The manufacturing landscape is constantly evolving, and as industries grow increasingly specialized, the need for high-quality precision tube making equipment becomes more prominent. Precision tubes are critical components used across various sectors, including automotive, aerospace, medical, and industrial applications. The sophistication of these tubes dictates the performance and reliability of the end products, necessitating advancements in the equipment used to produce them. In this article, we will delve into the latest innovations in precision tube making equipment, examine their applications, and explore future trends that may shape the industry for years to come.
At the heart of precision tube manufacturing is the need for accuracy and consistency in the production process. Traditional tube making methods often involve mechanical processes that can be labor-intensive and prone to human error. However, the rise of automation and advanced technologies has revolutionized the way precision tubes are produced. Modern precision tube making equipment integrates state-of-the-art technology such as CNC (Computer Numerical Control) machining, laser cutting, and advanced welding techniques, enabling manufacturers to achieve tight tolerances and superior surface finishes.
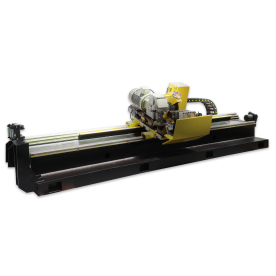
Exploring the Latest Innovations in Precision Tube Making Equipment: Advancements, Applications, and Future Trends
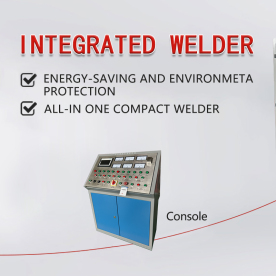
Exploring the Latest Innovations in Precision Tube Making Equipment: Advancements, Applications, and Future Trends
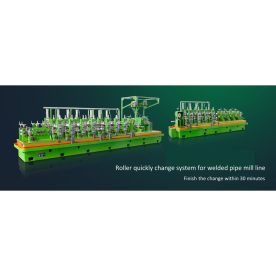
Exploring the Latest Innovations in Precision Tube Making Equipment: Advancements, Applications, and Future Trends
Moreover, precision tubes are increasingly being utilized in renewable energy applications, particularly in solar and wind technologies. These industries require tubes that can withstand harsh environmental conditions and high-stress loads, showcasing the need for equipment that can produce tubes capable of meeting such demanding specifications.
Looking to the future, several trends are likely to shape the precision tube making equipment market. One such trend is the growing emphasis on sustainability and eco-friendly manufacturing practices. As industries seek to reduce their carbon footprint, manufacturers of precision tube making equipment are focusing on developing machines that minimize waste and consume less energy. This includes innovations in the use of recyclable materials, cleaner production processes, and energy-efficient machinery.
Additionally, the integration of Industry 4.0 technologies, such as IoT (Internet of Things) and AI (Artificial Intelligence), is set to further revolutionize precision tube making. These technologies allow for real-time monitoring and data analysis, enabling manufacturers to optimize their processes, predict maintenance requirements, and enhance overall productivity. The predictive capabilities of AI will lead to smarter production lines, where adjustments can be made proactively to avoid potential issues before they arise.
In conclusion, the landscape of precision tube making equipment is undergoing significant transformation, driven by advancements in technology and evolving industry demands. With innovations such as CNC machining, laser cutting, and the integration of smart technologies, manufacturers can produce high-quality precision tubes that meet the rigorous standards of various applications. As sustainability and efficiency become increasingly critical, the future of precision tube making equipment holds the promise of an even more advanced and responsible manufacturing landscape.