[Spare parts for Solid state HF welder]Essential Guide to Sourcing Spare Parts for Solid State HF Welders: A Comprehensive Overview for Maintenance and Repair
News 2024-12-11
****Solid state high-frequency (HF) welders are an essential tool in various industries, particularly in metalworking and plastics. These sophisticated devices are engineered for high precision and efficiency in joining materials, making them invaluable in manufacturing processes. However, like all machinery, solid state HF welders can experience wear and tear, necessitating the need for reliable spare parts to ensure optimal performance. In this article, we will explore the importance of sourcing spare parts for solid state HF welders, the common components that may require replacement, and tips for finding quality parts.
Understanding Solid State HF Welders
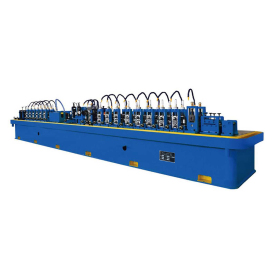
Essential Guide to Sourcing Spare Parts for Solid State HF Welders: A Comprehensive Overview for Maintenance and Repair
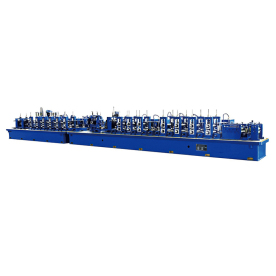
Essential Guide to Sourcing Spare Parts for Solid State HF Welders: A Comprehensive Overview for Maintenance and Repair
Why Spare Parts are Crucial
Regular maintenance and prompt replacement of worn components in solid state HF welders are vital for several reasons:
1. **Operational Efficiency**: Over time, components can break down or degrade, leading to inefficient operation. Replacing these parts can restore functionality and improve energy efficiency.
2. **Safety**: Malfunctioning equipment can pose safety risks to operators and bystanders. Ensuring that all components are in optimal condition mitigates these hazards.
3. **Cost-Effectiveness**: Investing in spare parts is generally more cost-effective than purchasing entirely new equipment. Repairs and part replacements can extend the life of your welder significantly.
4. **Performance Consistency**: Maintaining the integrity of your welding equipment ensures that you can achieve consistent results, which is crucial for quality assurance in production.
Common Spare Parts for Solid State HF Welders
There are several key components in solid state HF welders that are commonly replaced:
1. **Oscillator Modules**: The oscillator is responsible for generating the high-frequency signals that are essential for the welding process. If these modules fail, the welder will not operate effectively. Replacement typically involves sourcing compatible oscillator models.
2. **Capacitors**: These components store electrical energy and release it during the welding process. Over time, capacitors may degrade, impacting the welder's performance. It is vital to replace them with OEM (original equipment manufacturer) parts to ensure compatibility.
3. **High-Voltage Diodes**: These are critical for converting AC power to DC within the welder. Faulty diodes can lead to incomplete welding or equipment failure. Ensuring that you have quality replacements on hand is key.
4. **Cooling Fans and Heat Sinks**: Thermal management is essential to prevent overheating. Cooling fans that are inefficient can cause damage to internal components. Regular checks and timely replacement of these parts are necessary to maintain optimal operating conditions.
5. **Control Boards**: The control systems regulate various settings and functionalities of the welder. If there are issues with the control board, it can impact the operation of the entire machine. Finding a compatible replacement board is critical for restoring functionality.
Tips for Sourcing Spare Parts
When it comes to obtaining spare parts for solid state HF welders, consider the following strategies:
1. **OEM vs. Aftermarket**: OEM parts are often recommended because they are designed specifically for your model, ensuring seamless operation. Aftermarket parts may provide a more budget-friendly option but can vary in quality.
2. **Distributors and Suppliers**: Establish relationships with reputable distributors that specialize in welding equipment. They can provide guidance on the best parts for your specific model and often have access to a wide range of components.
3. **Online Resources**: Websites and forums dedicated to welding technology often have sections for spare parts, including classifieds for new and used components. This can be a great way to find rare or discontinued parts.

Essential Guide to Sourcing Spare Parts for Solid State HF Welders: A Comprehensive Overview for Maintenance and Repair
5. **Consultation with Professionals**: If unsure about what parts you need, consider consulting with professional welders or technicians. Their experience can be invaluable in making informed decisions.
Conclusion
Sourcing spare parts for solid state HF welders is crucial for maintaining the longevity, efficiency, and safety of your welding equipment. By understanding the essential components and adopting effective sourcing strategies, you can ensure that your welder remains operational and effective in all your manufacturing processes. Regular maintenance coupled with timely replacement of spare parts contributes to a reliable and cost-effective welding operation.