[Pipe making machine with welding function]Revolutionizing Pipe Production: The Advanced Pipe Making Machine with Welding Function for Enhanced Efficiency and Quality
News 2024-12-11
In the rapidly evolving world of manufacturing, technological advancements are continuously reshaping how products are made. One such remarkable innovation is the pipe-making machine with welding function, which has transformed the fabrication of pipes in various industries, including construction, oil and gas, plumbing, and more. This advanced machinery not only streamlines production processes but also ensures higher quality and more durable piping solutions. In this article, we will explore the features, benefits, and applications of pipe-making machines equipped with welding capabilities.
Understanding Pipe Making Machines with Welding Functions
A pipe making machine with welding function is specifically designed to produce pipes of various materials, including steel, stainless steel, aluminum, and PVC, depending on the machine's configuration. The core of this machinery is its ability to not only form but also join pipe sections through various welding techniques, such as high-frequency induction welding, TIG (Tungsten Inert Gas) welding, or MIG (Metal Inert Gas) welding.
The process typically begins with raw materials being fed into the machine, which then shapes them into a desired pipe profile. After forming, the edges of the formed strip are aligned and welded together, completing the pipe-making process in a seamless fashion. This integrated approach allows for faster production times and minimizes labor costs, making it an ideal choice for manufacturers looking to enhance their productivity.
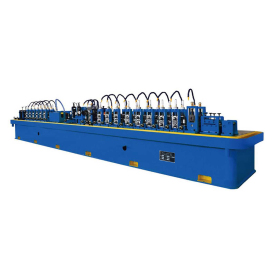
Revolutionizing Pipe Production: The Advanced Pipe Making Machine with Welding Function for Enhanced Efficiency and Quality
1. **Multifunctional Capabilities**: One of the primary advantages of these machines is their multifunctionality. They can produce pipes of various sizes and shapes and accommodate different welding techniques. This versatility enables manufacturers to meet diverse market demands.
2. **Automated Processes**: Modern pipe-making machines typically come equipped with advanced technology that allows for automation in the forming and welding processes. This automation reduces human error, ensures consistency in product quality, and lowers production costs over time.
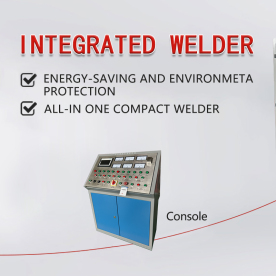
Revolutionizing Pipe Production: The Advanced Pipe Making Machine with Welding Function for Enhanced Efficiency and Quality
4. **Quality Control Features**: Advanced machines include built-in quality control systems that monitor welding temperatures, pressures, and finished product dimensions. This feature assures manufacturers of the high integrity and durability of the pipes produced.
5. **Ease of Maintenance**: Typically designed for operational efficiency, these machines also feature user-friendly interfaces and easy maintenance protocols. This results in reduced downtime and improved overall performance.
Benefits of Using Pipe Making Machines with Welding Functions
The integration of welding functions in pipe-making machines provides several benefits to manufacturers:
1. **Cost-Effectiveness**: As a result of increased production speeds and reduced labor requirements, these machines represent a cost-effective investment in modern manufacturing. They can produce a higher volume of superior-quality pipes in less time, boosting overall profitability.
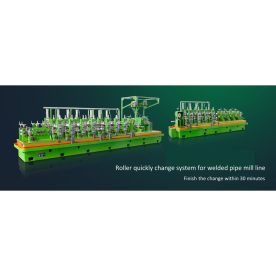
Revolutionizing Pipe Production: The Advanced Pipe Making Machine with Welding Function for Enhanced Efficiency and Quality
3. **Flexibility in Production**: With capabilities to switch between different pipe specifications rapidly, these machines allow manufacturers to adapt to changing market demands without the need for extensive downtimes or additional equipment investments.
4. **Increased Market Competitiveness**: By using state-of-the-art pipe making machines with welding functions, manufacturers can offer superior products faster than competitors who still rely on traditional piping production methods.
Applications in Various Industries
Pipe making machines equipped with welding functions have widespread applications across numerous sectors:
- **Construction**: These machines are essential in creating structural pipes used in building frameworks. - **Oil and Gas**: They manufacture durable pipes for transporting oil and gas safely. - **Plumbing**: The reliability of welded pipes makes them ideal for water supply and drainage systems. - **Agriculture**: They produce irrigation pipes that withstand high pressure and wear.
Conclusion
The pipe-making machine with welding function represents a major leap forward in manufacturing technology, enabling companies to produce high-quality pipes efficiently and cost-effectively. As industries continue to evolve, embracing this advanced technology is an essential step for manufacturers seeking competitive advantages in quality, production speed, and overall operational efficacy. By investing in a pipe-making machine with integrated welding functions, businesses not only secure their place in the market but also contribute to a more efficient, sustainable future in manufacturing.