[Industrial Cold Cutting Saw Machine]Exploring the Benefits and Applications of the Industrial Cold Cutting Saw Machine in Modern Manufacturing Processes
News 2024-12-11
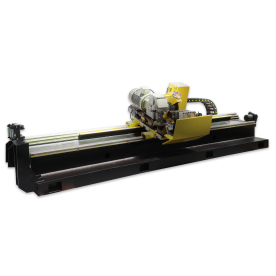
Exploring the Benefits and Applications of the Industrial Cold Cutting Saw Machine in Modern Manufacturing Processes
The Industrial Cold Cutting Saw Machine operates using a series of high-speed, rotating blades that cut through metal and other materials swiftly and accurately. Unlike traditional saws that rely on heat generation from friction, cold cutting machines utilize a unique cooling system that minimizes temperatures during the cutting process. This distinction not only prolongs the lifespan of the blade but also improves the quality of the cut.
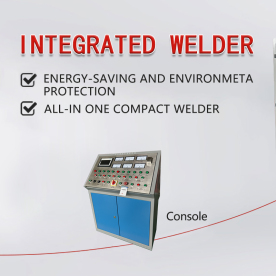
Exploring the Benefits and Applications of the Industrial Cold Cutting Saw Machine in Modern Manufacturing Processes
1. **Heat Management**: One of the most significant advantages of the Industrial Cold Cutting Saw Machine is its ability to manage heat. Excessive heat in traditional cutting processes can lead to warped materials and diminished quality. The cooling system in cold cutting saws ensures that the cutting surface remains cool, which is vital for materials that are sensitive to temperature changes. This heat management significantly reduces the chances of metallurgical changes in the material being cut, ensuring that the integrity and properties of the metal are preserved.
2. **Precision and Clean Cuts**: Precision is crucial in manufacturing environments where tolerances are tight. The Industrial Cold Cutting Saw Machine provides a level of accuracy that traditional saws often struggle to achieve. It ensures clean cuts with minimal burrs, eliminating the need for secondary finishing processes. This capability is particularly beneficial when cutting intricate shapes or when working with delicate materials that require a high-quality finish.
3. **Efficiency and Speed**: With advancements in technology, Industrial Cold Cutting Saw Machines are designed to operate at higher speeds without compromising quality. This speed not only enhances productivity but also minimizes material waste, as precise cuts reduce the overall scrap generated in the cutting process. The combination of speed and precision makes these machines invaluable in high-volume manufacturing settings.

Exploring the Benefits and Applications of the Industrial Cold Cutting Saw Machine in Modern Manufacturing Processes
5. **Enhanced Safety**: Safety is always a priority in industrial settings. The Industrial Cold Cutting Saw Machine reduces the risk of accidents associated with heat burns and flying debris. The cooling mechanism and enclosed cutting environment ensure a safer workspace for operators, making these machines a smart choice for companies prioritizing worker safety.
Applications
The Industrial Cold Cutting Saw Machine finds applications across various sectors. In the construction industry, it is used to cut steel beams, pipes, and other structural materials with accuracy. The automotive industry benefits by using these machines to cut components with stringent tolerances, ensuring that parts fit together seamlessly.
Metal fabricators have adopted cold cutting saws for their efficiency in processing metal sheets and profiles. HVAC manufacturers also utilize these machines to obtain precise cuts for ductwork and fittings, highlighting the machine's flexibility across different applications.
In conclusion, the Industrial Cold Cutting Saw Machine represents a significant advancement in the manufacturing process, offering numerous benefits that drive productivity, safety, and quality. As industries continue to seek ways to improve their operations, the adoption of this technology is likely to increase, making it a critical asset in the modern manufacturing landscape. Companies looking to enhance their cutting capabilities should consider investing in this innovative tool, positioning themselves at the forefront of industry advancements and ensuring long-term competitiveness in a rapidly changing market.