[Tube Mill Replacement Parts]Essential Guide to Tube Mill Replacement Parts: Ensuring Optimal Performance and Longevity for Your Manufacturing Equipment
News 2024-12-10
In the world of manufacturing, productivity and efficiency are paramount. One of the key components of many production lines is the tube mill, a type of machinery used to produce tubular products from a variety of materials. Over time, tube mills experience wear and tear due to the demands of continuous operation, which can lead to decreased performance and, ultimately, unplanned downtimes. In such cases, having a reliable source for tube mill replacement parts becomes crucial. This article provides a comprehensive guide to understanding tube mill replacement parts, their importance, and how to ensure you have the right ones for your specific manufacturing needs.
The Importance of Tube Mills in Production
Tube mills play an essential role in the production of steel tubes, pipes, and various other tubular products used in multiple industries, including construction, automotive, and energy. The ability to form, weld, and cut materials into precise specifications makes tube mills invaluable. However, like all machinery, they are subject to wear from high-speed operations and the inherent stresses of processing metals.
Common Wear Parts of Tube Mills
Understanding the specific components of a tube mill that may require replacement is crucial for effective maintenance. Here are some of the most common parts that may wear out and need replacing:
1. **Rolls**: The rolls are critical in shaping the material. They endure the most stress and can wear down over time. If they become too worn, they can lead to defects in the products being produced.
2. **Weld Heads**: These parts are essential for the welding of tube seams. They can degrade due to heat and pressure, leading to poor-quality seams that may compromise product integrity.
3. **Guides and Supports**: These components help to maintain the alignment and positioning of the material as it passes through the mill. Misalignments can cause defects and compromise overall productivity.
4. **Bearings**: Bearings support rotating components. Over time, they may develop issues such as noise, vibration, or excessive wear, leading to poor performance.
5. **Drives and Motors**: The motors provide the necessary power for the tube mill operation. An issue with the drive can lead to insufficient power delivery, affecting output.
Benefits of Quality Replacement Parts
Choosing quality tube mill replacement parts is crucial for ensuring that your equipment runs smoothly. Here are some of the key benefits:
- **Enhanced Performance**: Quality parts are designed and manufactured to meet or exceed OEM (Original Equipment Manufacturer) standards, ensuring that your tube mill operates at peak efficiency.
- **Increased Longevity**: Investing in high-quality replacement parts contributes to the overall longevity of your equipment, reducing the frequency of repairs and downtime.
- **Cost-Effectiveness**: While quality parts may involve a higher initial investment, they often lead to lower maintenance and operational costs over time. The less frequent need for replacements can save valuable resources and reduce labor costs.
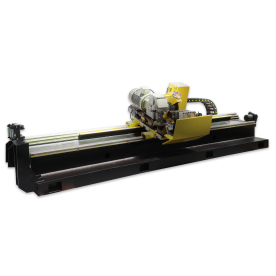
Essential Guide to Tube Mill Replacement Parts: Ensuring Optimal Performance and Longevity for Your Manufacturing Equipment
When it comes to sourcing tube mill replacement parts, it is essential to work with a reputable supplier who understands the specific needs of your equipment. Here are some steps to ensure you find the right parts:

Essential Guide to Tube Mill Replacement Parts: Ensuring Optimal Performance and Longevity for Your Manufacturing Equipment
2. **Research Suppliers**: Look for suppliers who specialize in tube mill parts. Expertise can make a significant difference in finding high-quality components.
3. **Inquire About Options**: Many suppliers offer both OEM and aftermarket parts. Consider the benefits of each type to determine which will suit your operation best.
4. **Check Reviews and Testimonials**: Researching customer experiences can provide insight into the reliability and performance of the parts being offered.
Regular Maintenance and Inspection
Proactive maintenance and inspection of tube mills can make a significant impact in mitigating the need for frequent replacement parts. Regular checks can identify early signs of wear and prevent major failures, allowing for timely replacements before they affect production.
Conclusion
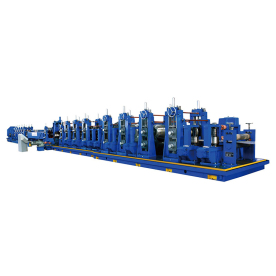