[High frequency welder equipment]Understanding High Frequency Welder Equipment: How It Revolutionizes Welding Processes in Various Industries
News 2024-12-9
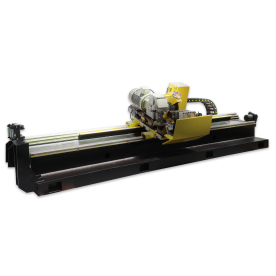
Understanding High Frequency Welder Equipment: How It Revolutionizes Welding Processes in Various Industries
What is High Frequency Welding?
High frequency welding, also known as high frequency induction welding, utilizes electromagnetic waves to produce heat in the workpieces being joined. The process often employs specific high frequency welder equipment that generates a high frequency electromagnetic field, inducing heat in the metal without direct contact. This heat is sufficient to create a strong weld joint in the materials being processed.
The technology typically operates in the frequency range of 1 MHz to 150 MHz, allowing for rapid heating and welding of various materials. It is particularly effective for joining thinner materials, such as steel and aluminum, making it an invaluable tool in many manufacturing applications.
Applications of High Frequency Welder Equipment
High frequency welder equipment finds its application across a range of industries, including:
1. **Pipe and Tube Manufacturing**: One of the notable applications is in the production of pipes and tubes. The welding process allows for high-speed production while ensuring high-quality weld seams. It is particularly useful in creating welded tubes for oil and gas industries, as well as automotive sectors.
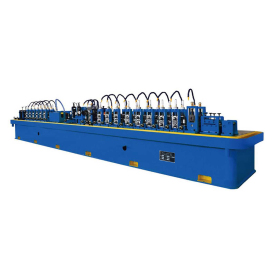
Understanding High Frequency Welder Equipment: How It Revolutionizes Welding Processes in Various Industries
3. **Textile Industry**: In the textile sector, high frequency welding is utilized to bond materials such as PVC and other synthetics. This application helps in manufacturing waterproof and durable products like tarps, banners, and inflatable structures.
4. **Packaging Industry**: High frequency welders are increasingly used in the packaging sector for creating airtight seals in flexible packaging materials. This enhances product shelf life while reducing waste.
Advantages of High Frequency Welder Equipment
The growing popularity of high frequency welding can be attributed to several key advantages:
1. **Speed and Efficiency**: High frequency welding allows for rapid processing, significantly reducing production times. The ability to quickly generate heat and create welds translates into higher outputs and better overall productivity.
2. **High-Quality Welds**: The precision involved in high frequency welding ensures clean and uniform welds. The lack of contamination during the welding process further enhances the integrity of the weld seams.
3. **Cost-Effective**: While the initial investment in high frequency welder equipment may be significant, the long-term benefits often outweigh those costs. The efficiency and reduced need for manual labor translate into significant savings over time.
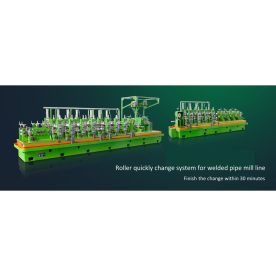
Understanding High Frequency Welder Equipment: How It Revolutionizes Welding Processes in Various Industries
The Future of High Frequency Welder Equipment
As technology advances, high frequency welder equipment is expected to continue evolving, incorporating smart technologies and automation. The integration of artificial intelligence and IoT (Internet of Things) capabilities could lead to enhanced monitoring and control of the welding process, further optimizing performance and safety.
Additionally, as industries seek more sustainable production methods, high frequency welding aligns well with these objectives due to its energy efficiency compared to traditional methods. The growing emphasis on environmentally friendly practices is likely to drive the adoption of this technology.
Conclusion
High frequency welder equipment represents a significant advancement in welding technology, offering numerous benefits across various sectors. Its ability to produce high-quality welds quickly and efficiently makes it a vital tool for manufacturers striving to meet modern demands. As industries continue to evolve, the importance of reliable and efficient welding solutions ensures that high frequency welding will remain at the forefront of manufacturing innovation for years to come.