[High-power Solid state HF welder ]Exploring the Advantages and Applications of High-Power Solid State HF Welder in Modern Industrial Manufacturing
News 2024-12-9
In the ever-evolving landscape of industrial manufacturing, the quest for efficiency and precision drives the adoption of innovative technologies. High-power solid state HF welders have emerged as a significant advancement in the sphere of welding technology, offering enhanced performance features that cater to the demands of various industries. This article delves into the operational principles, benefits, applications, and future prospects of these powerful welding systems.
Understanding High-Power Solid State HF Welders
High-frequency (HF) welding is a method that utilizes electromagnetic energy to join materials. Traditionally, this technology relied on vacuum tube technology to generate the high-frequency waves needed for welding processes. However, the advent of solid-state technology has revolutionized the field. High-power solid state HF welders employ semiconductor devices to produce the necessary high-frequency signals, making them more efficient, reliable, and compact compared to their tube-based counterparts.
These modern welders operate by converting electrical energy into high-frequency electromagnetic energy, which generates heat upon contact with the materials being joined. The solid-state design allows for rapid adjustments in power levels and frequency, making the welding process adaptable to different materials and thicknesses.
Advantages of High-Power Solid State HF Welders
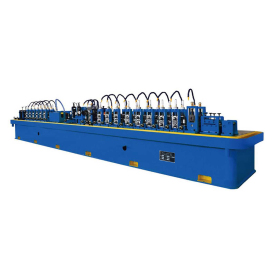
Exploring the Advantages and Applications of High-Power Solid State HF Welder in Modern Industrial Manufacturing
2. **Improved Weld Quality**: Consistent control over the welding parameters ensures high-quality welds. Solid-state HF welders provide better stability and precision, minimizing defects and enhancing the overall structural integrity of the welded components. This is especially critical when working with thin materials or fabrics where precision impacts performance.
3. **Compact Design and Portability**: The solid-state technology fosters a more compact design compared to traditional welding systems. This makes high-power solid state HF welders easier to integrate into existing workflows and more convenient for operation in tight spaces. Moreover, their lightweight nature enhances portability, allowing for greater flexibility in industrial applications.
4. **Durability and Reliability**: Solid-state components are typically more durable than vacuum tubes, which are prone to wear and failure. Welders using solid-state technology have longer lifespans and require less maintenance, leading to reduced downtime and operational costs. Additionally, these systems can operate in harsher environments due to their robust construction.
Applications Across Industries
High-power solid state HF welders are utilized in a diverse range of industries due to their versatility in handling different materials such as plastics, metals, and composites. One notable application is in the automotive sector, where they are employed for joining components in manufacturing processes, facilitating the production of lightweight and fuel-efficient vehicles.
In the packaging industry, high-frequency welding is leveraged for producing high-quality seals in plastic materials. The ability of solid state HF welders to create strong, uniform seals ensures the long-term preservation of goods.
Additionally, the textile and fashion industries benefit from these welders, as they enable the seamless joining of synthetic fabrics, enhancing aesthetic appeal while maintaining the integrity of the materials. Other sectors, such as electronics and construction, are also reaping the benefits of solid-state HF welding technology.
Future Trends and Innovations
As technology progresses, the future of high-power solid state HF welders looks promising. Innovations in control systems and automation will likely lead to even greater efficiency and precision. Integrating artificial intelligence and machine learning into welding processes could enable real-time monitoring and adjustment, further enhancing weld quality.
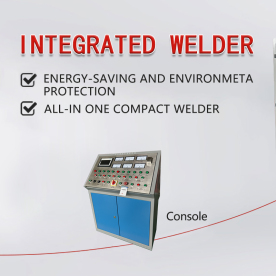
Exploring the Advantages and Applications of High-Power Solid State HF Welder in Modern Industrial Manufacturing

Exploring the Advantages and Applications of High-Power Solid State HF Welder in Modern Industrial Manufacturing
High-power solid state HF welders represent a significant leap forward in welding technology, providing unparalleled efficiency, precision, and durability. Their widespread applications across various industries underscore their importance in modern manufacturing. As we look towards the future, the continued evolution of this technology promises to meet the growing demands of an increasingly competitive industrial landscape while fostering sustainable practices. Embracing these advancements will undoubtedly enhance productivity and quality in the manufacturing sector for years to come.