[High frequency welder for plastic]Exploring the Advantages and Applications of High Frequency Welders for Plastic in Modern Manufacturing Processes
News 2024-12-9
****In today’s fast-paced manufacturing environment, the need for efficient, reliable, and precise welding methods is crucial. High frequency welders for plastic have emerged as a vital solution, particularly in industries where plastic materials are predominant. This article will explore the technology behind high frequency welding, its benefits, and its various applications across different sectors.
Understanding High Frequency Welding
High frequency welding, also known as radio frequency (RF) welding or dielectric welding, is a process in which polyester or other thermoplastic materials are fused together using an electromagnetic field. The high-frequency electromagnetic waves generate heat through dielectric heating, causing the polymer chains within the plastic to mobilize and bond when they are pressed together.
The process is highly effective for materials that cannot be welded using traditional techniques such as laser or hot-air welding, particularly due to their molecular structure. High frequency welding is prevalent in applications where a strong, airtight seal is required, which is essential for products that must retain their integrity under pressure or contain sensitive materials.
Advantages of High Frequency Welding for Plastic
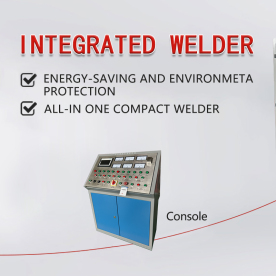
Exploring the Advantages and Applications of High Frequency Welders for Plastic in Modern Manufacturing Processes
2. **Strong and Durable Seals**: The electromagnetic welding method creates strong bonds that can withstand stress and strain. This is particularly crucial in applications such as inflatable products, medical devices, and other high-pressure items where a leak-free seal is mandatory.
3. **Versatility**: High frequency welders are suitable for a wide range of plastic materials, including PVC, TPU, and LDPE. This versatility allows manufacturers to produce a diverse array of products, from durable outdoor equipment and tarps to healthcare items like IV bags and surgical supplies.
4. **No Additional Materials Required**: Unlike other welding methods that may necessitate the use of adhesives or additional bonding materials, high frequency welding achieves a bond purely through the application of heat and pressure. This results in a cleaner, more efficient process that reduces waste and the risk of contamination.
5. **Cost-Effectiveness**: Although the initial investment in high frequency welding machinery can be substantial, the long-term savings in labor costs, material efficiency, and reduced scrap rates generally justify the expenditure. The ability to produce robust products quickly can lead to higher profitability.
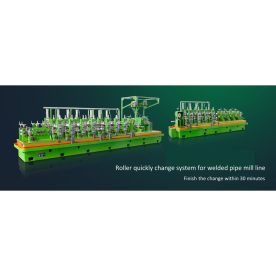
Exploring the Advantages and Applications of High Frequency Welders for Plastic in Modern Manufacturing Processes

Exploring the Advantages and Applications of High Frequency Welders for Plastic in Modern Manufacturing Processes
Applications of High Frequency Welding
The applications of high frequency welding span various industries, including:
- **Textiles and Apparel**: High frequency welding is commonly used in the production of waterproof clothing and gear, as well as in the joining of technical fabrics for specialized applications.
- **Packaging**: Many packaging solutions, especially flexible packaging for food and pharmaceuticals, utilize high frequency welding. Its ability to create airtight seals is essential for maintaining product freshness and extending shelf life.
- **Automotive**: In the automotive sector, high frequency welders are employed for creating various components, from upholstery to inflatable safety features, due to the robust bonding characteristics.
- **Medical Devices**: The medical industry benefits significantly from high frequency welding, especially for items such as bags, tubing, and other disposable devices that require sterile integrity.
- **Inflatable Products**: High frequency welding is the preferred method for creating inflatable items such as tents, pool toys, and life jackets, where a leak-free experience is vital.
Conclusion
High frequency welders for plastic represent a significant advancement in welding technology, providing manufacturers with a reliable, efficient, and versatile method for joining thermoplastic materials. As the demand for innovative products continues to grow, the role of high frequency welding in various industries will undoubtedly expand. Understanding this technology will enable businesses to optimize their operations, improve product quality, and enhance their competitive edge in the market.