[Portable high frequency welder]Exploring the Versatile Applications and Advantages of Portable High Frequency Welders in Modern Manufacturing and Repair Industries
News 2024-12-9
In recent years, the demand for efficient, reliable, and portable welding solutions has surged across various sectors, from automotive to electronics. One advanced tool that has gained significant traction in these industries is the portable high frequency welder. This versatile device boasts numerous advantages, making it a sought-after solution in modern manufacturing and repair applications. In this article, we will delve into what portable high frequency welders are, their unique features, benefits, and how they have revolutionized welding practices.
Understanding Portable High Frequency Welders
A portable high frequency welder is an electrical device designed for resistance welding processes characterized by the application of high-frequency electrical currents. This type of welder is particularly advantageous for applications where traditional welding might be cumbersome or impractical due to space or accessibility issues.
Portable high frequency welders utilize high-frequency oscillators to create an electrical field, which generates heat in conductive materials, allowing for precision welding without needing direct contact. This innovative process enables welders to join a variety of materials efficiently, from metals to thermoplastics.
Key Features of Portable High Frequency Welders
1. **Compact Design**: As indicated by the term "portable," these welders are designed to be lightweight and compact, facilitating easy transportation and use in tight spaces or remote locations. This feature is particularly beneficial for on-site repairs or installations, where access to power sources may be limited.
2. **Versatility**: Portable high frequency welders can be employed across a broad range of materials and thicknesses, making them useful in various industries. Whether working with soft metals, plastics, or composites, this type of welder can adapt to different welding needs.
3. **User-Friendly Operation**: Many modern portable high frequency welders come equipped with intuitive controls and settings that simplify the welding process. Users can easily adjust parameters such as frequency, power, and welding time, ensuring optimal results without extensive training.
4. **Energy Efficiency**: The high-frequency technology used in these welders often leads to reduced energy consumption compared to traditional welding techniques. This efficiency can contribute to lower operational costs and a reduced environmental footprint, making portable high frequency welders an eco-friendly choice.
Advantages of Using Portable High Frequency Welders
1. **Time-Saving**: The fast heating and cooling times involved in high frequency welding lead to shorter welding cycles. This characteristic can significantly enhance productivity, allowing businesses to complete projects more rapidly.
2. **Precision and Quality**: The ability to control the welding parameters results in high-quality welds with minimal defects. This precision is crucial, especially in applications such as electronics, where the integrity and reliability of connections are paramount.
3. **Low Heat Input**: High frequency welding generates heat primarily within the materials being joined, minimizing the heat affected zone and reducing the risk of warping or damage to adjacent areas. This attribute is essential when welding thin materials or those sensitive to heat.
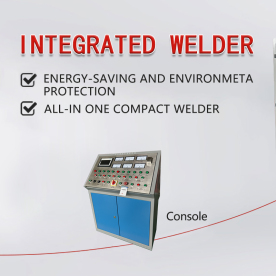
Exploring the Versatile Applications and Advantages of Portable High Frequency Welders in Modern Manufacturing and Repair Industries
5. **Operational Flexibility**: The portability of these welders allows them to be used in various settings, from manufacturing plants to small workshops and field service operations. This capability provides businesses with great flexibility in their operations.
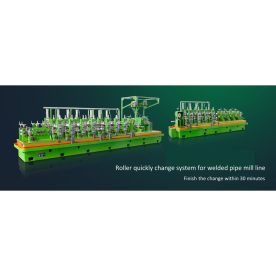
Exploring the Versatile Applications and Advantages of Portable High Frequency Welders in Modern Manufacturing and Repair Industries

Exploring the Versatile Applications and Advantages of Portable High Frequency Welders in Modern Manufacturing and Repair Industries
Portable high frequency welders are employed in diverse areas, including:
- **Automotive**: For welding components like battery packs, wiring harnesses, and body parts where precision is critical. - **Electronics**: In the assembly of circuit boards and components where heat damage must be minimized. - **Textiles and Fabrics**: For joining coated fabrics and welding seams in protective clothing or industrial textiles. - **Packaging**: For creating seals in flexible packaging materials.
Conclusion
The portable high frequency welder stands out as a cutting-edge solution in the welding industry, marrying efficiency and precision with portability. As businesses continuously seek ways to enhance productivity while maintaining quality, the adoption of such advanced technology will likely increase. With its myriad advantages, the portable high frequency welder is set to redefine welding practices in various industries, fostering innovation and excellence in manufacturing and repair processes.