[Industrial All-in-one High Frequency Welder]Maximizing Production Efficiency with Industrial All-in-One High Frequency Welder: A Comprehensive Guide for Modern Manufacturing
News 2024-12-5
****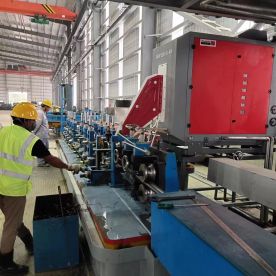
Maximizing Production Efficiency with Industrial All-in-One High Frequency Welder: A Comprehensive Guide for Modern Manufacturing
**Understanding the Functionality of an Industrial All-in-One High Frequency Welder**

Maximizing Production Efficiency with Industrial All-in-One High Frequency Welder: A Comprehensive Guide for Modern Manufacturing
One of the distinguishing features of these welders is their ability to operate on multiple welding processes. This includes, but is not limited to, high-frequency induction welding, RF (radio frequency) welding, and dielectric heating. The incorporation of numerous functions allows manufacturers to consolidate equipment, reducing the need for multiple machines while increasing the efficiency of their operations.
**Advantages of Implementing an Industrial All-in-One High Frequency Welder**
1. **Enhanced Precision and Quality:** High-frequency welding technology offers a high level of control over the weld process, which results in stronger joints and higher quality finishes. The precision delivered by these welders is crucial, particularly in industries where structural integrity is vital.
2. **Increased Speed and Efficiency:** With advanced technology, these welders significantly reduce the time needed for welding processes. High-frequency welders can complete welding in a fraction of the time compared to traditional methods, thereby ramping up production speed. The time saved directly translates to cost savings, providing a competitive edge in fast-paced markets.
3. **Versatile Applications:** The adaptability of the Industrial All-in-One High Frequency Welder is one of its primary advantages. Whether it’s welding complex automotive parts or creating intricate designs in textiles, this welder can handle diverse materials with ease. This versatility eliminates the need for multiple specialized machines, consolidating operations and reducing overhead costs.
4. **Reduced Material Waste:** Traditional welding methods often involve significant waste in terms of materials and time. High-frequency welding, on the other hand, can achieve cleaner and tighter joints, minimizing the amount of excess material needed and thereby reducing overall waste.
5. **Energy Efficiency:** These modern welders are designed with energy-efficient technologies that consume less power while delivering high performance. This not only lowers operating costs but also aligns with the growing demand for sustainable manufacturing practices.
**Implementing Industrial All-in-One High Frequency Welders in Operations**
Adopting Industrial All-in-One High Frequency Welders into an organization's operations involves several considerations. First and foremost, training personnel is crucial to ensure skilled handling of the technology. Regular maintenance and calibration are also required to maximize the equipment's lifespan and performance.
Additionally, it’s important for companies to analyze their specific needs and assess the return on investment (ROI) associated with such machinery. While the initial capital outlay can be significant, the benefits of increased efficiency, reduced waste, and heightened quality usually outweigh the costs in the long term.
